Discover all the features of
Exteryo Safety 4.0
Everything You Need to Know About Company Management Software
Index
1. INTRODUCTION
1.1 WELCOME TO THE TUTORIAL FOR THE USE OF THE EXTERYO SAFETY 4.0 PLATFORM
In this guide, we will explain to you step by step how to use the Exteryo Safety 4.0 software for company safety management
Once you have mastered the basics of the system, you will be able to carry out your work quickly and accurately, with great benefits for your business.
1.2. SMARTPHONE, TABLET OR COMPUTER?
The ES4.0 platform can be used both via smartphone or tablet and via computer. The application for smartphones and tablets is available for both Apple and Android. Click on the icon you prefer to get access to our Exteryo Safety 4.0 application
1.3. UNIQUE CODE OR DIGITAL IDENTIFICATION?
The Exteryo Safety 4.0 system for the management of physical products (PPE, workwear, lifeline components, etc.) can be used either in “smart” mode, through the use of appropriate Digital Identifiers (NFC technology tags or QRcodes), or in analogue mode with the manual entry of unique codes for individual devices.
The functionality of the software is identical with both methods, although the use of digital identifiers allows for quick association and reading of information relating to individual devices, also reducing the risk of human error in compilation.
If you intend to use digital identifiers with NFC technology, you will first need a smartphone with this technology (click here for a complete list) or a special NFC reader that can be connected to your computer via a USB port or to your tablet via a reduction from standard USB to USB type B or type C.
If you have an ANDROID smartphone, in order to read an NFC tag via your smartphone, you have to activate the NFC functionality on your smartphone (settings-connectivity-NFC) and after unlocking your smartphone, simply place the back of the chip on it to activate communication.
If, on the other hand, you have an APPLE smartphone, the NFC functionality is active by default, so within the application you simply click on the read button and then place the back of the smartphone on the NFC tag.
1.4 NFC TAGS, WHERE TO FIND THEM?
NFC tags are available in different solutions that can be used according to the type of PPE on which they are to be inserted. The manufacturing companies that are partners in the system already fit NFC tags that are attached to the PPE in a solid manner within a wide range of products. If your PPE does not have an NFC tag, you can easily insert one by choosing from the various solutions offered by Exteryo and its resellers. Contact your dealer for a catalogue of NFC chips, or write to customer@exteryo.com.
2. ACCESS TO THE PLATFORM
2.1 ACCESSING THE SOFTWARE WITH CREDENTIALS
You can use the Exteryo Safety 4.0 platform either via your smartphone or tablet or via a PC.
Let’s see below how to access the platform in the two different modes:
ACCESS VIA SMARTPHONE/TABLET
To access via smartphone or tablet, simply open the app on your device and you will be immediately directed to the Log-in page where you can enter your access credentials.
Three codes are required
– LICENCE CODE
– USERNAME
– PASSWORD
When the licence admin has created your user name, you will receive your login credentials by email.
ACCESS VIA PC
To log in via PC, you need to connect to the www.exteryo-safety.com website and click on the LOG IN button at the top of the screen.
The Log-in page will then appear and you can follow the instructions above to log in.
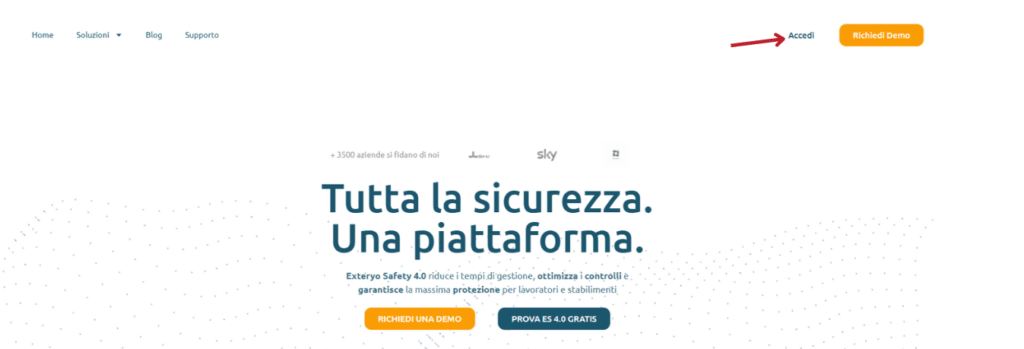
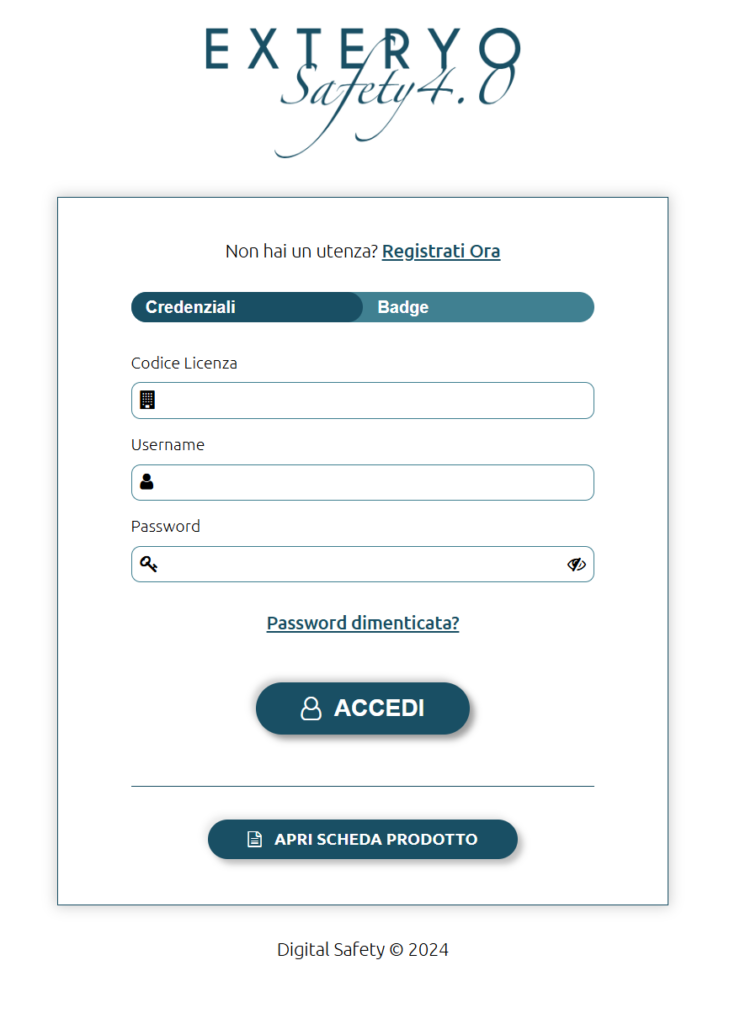

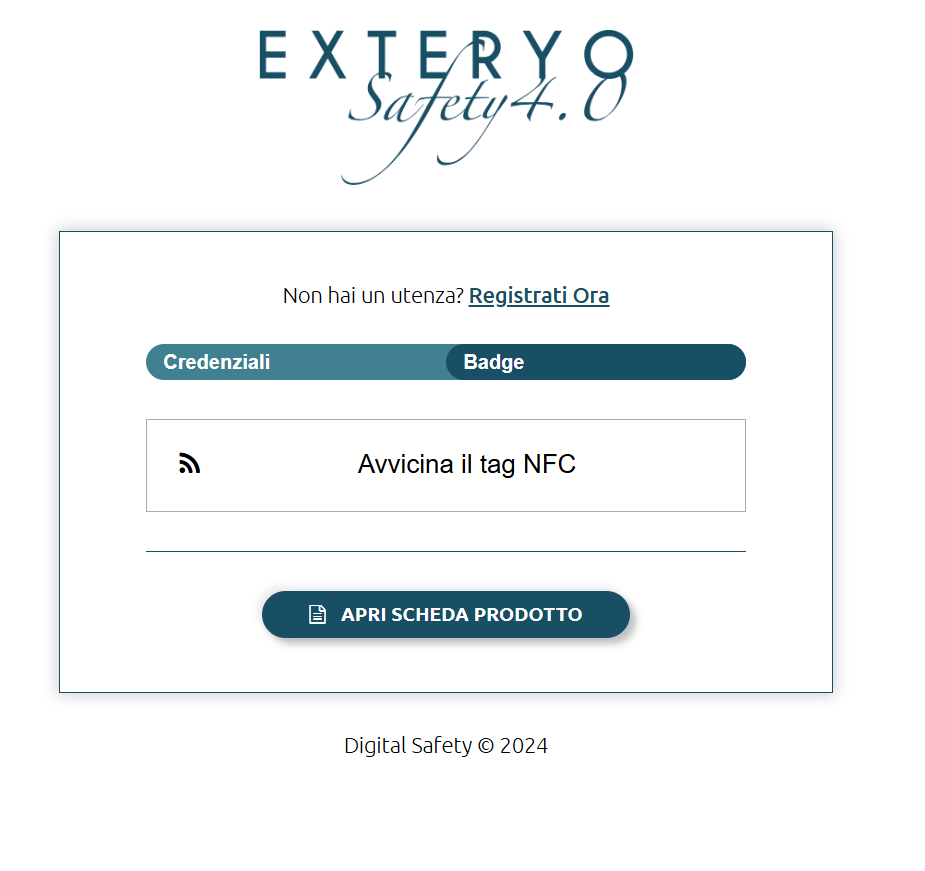
2.2 ACCESS TO THE SOFTWARE VIA BADGE
To speed up access to the platform, you can use your COMPANY BADGE for quick recognition, either from a smartphone/tablet or from a PC.
To use this option, your badge must first have been associated with your user account (see WORKERS REGISTRY section).
Once you have enabled the badge to your user account, you can click on the BADGE button in the Log-In section and read your badge by placing it on the back of your smartphone/tablet (NFC function) or on the PC badge reader.
2.3 FORGOTTEN PASSWORD
Should you forget your password, you can request our support by clicking the FORGOTTEN PASSWORD button on the Log-IN page.
By entering your LICENCE CODE and your EMAIL ADDRESS, you will be sent a communication with the new password generated.
Once you have logged in, you will be able to change your password under USER OPTIONS.
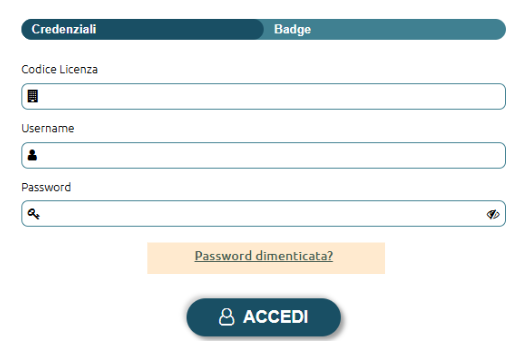
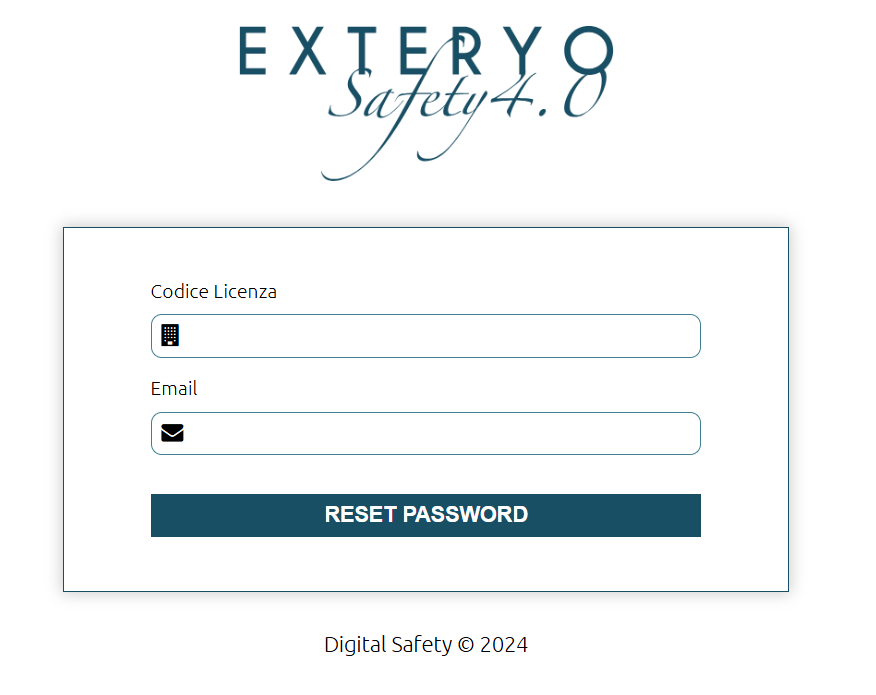
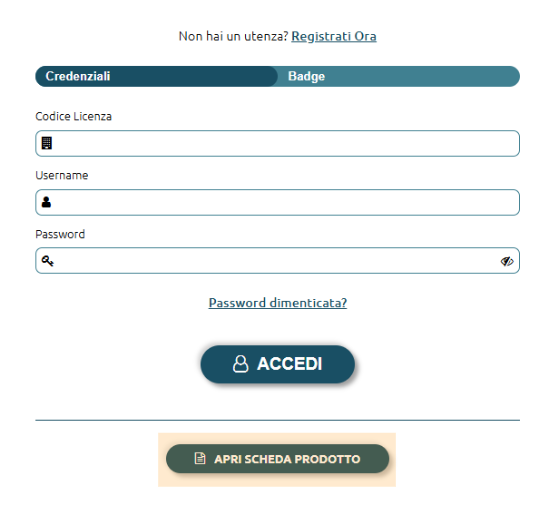

2.4 "OPEN PRODUCT SHEET" FUNCTION
The “OPEN PRODUCT SHEET” button, located at the bottom of the Log-in window, allows a user without access credentials to view the data of a product (PPE, KIT, Plant or Fall Protection System Component). For privacy reasons, the data of the company owning or possibly using the product are not available, but product-specific data, its status or technical documentation can be viewed.
To view the product data, simply read the digital identifier (NFC/QRcode) via smartphone/tablet or special PC reader
3. GENERAL ORGANISATION OF THE PLATFORM
3.1 STRUCTURE OF THE SYSTEM
Once logged in, you can access the programme’s DASHBOARD.
The structure of the platform is organised into two main sections that can be defined as follows
TOP BAR: this is the menu in which the macro-areas of operation of the platform (Dashboard, PPE, Fall Protection Systems, etc.) are presented.
The right-hand side of the manage board also contains the GENERAL SETTINGS, TUTORIAL access and SUPPORT buttons.
SIDE MENU: this is the platform menu where it is possible to select the functions for using the platform.
The functions of the side menu vary depending on the macro-area selected within the manage board.
At the top of the FUNCTIONALITIES MENU’ it is possible to access the USER OPTIONS by clicking the button positioned below your user name.
Instead, by clicking the button it is possible to log out of the platform.
Finally, by clicking the button you can fix or hide the FUNCTIONALITIES MENU’ according to your needs.
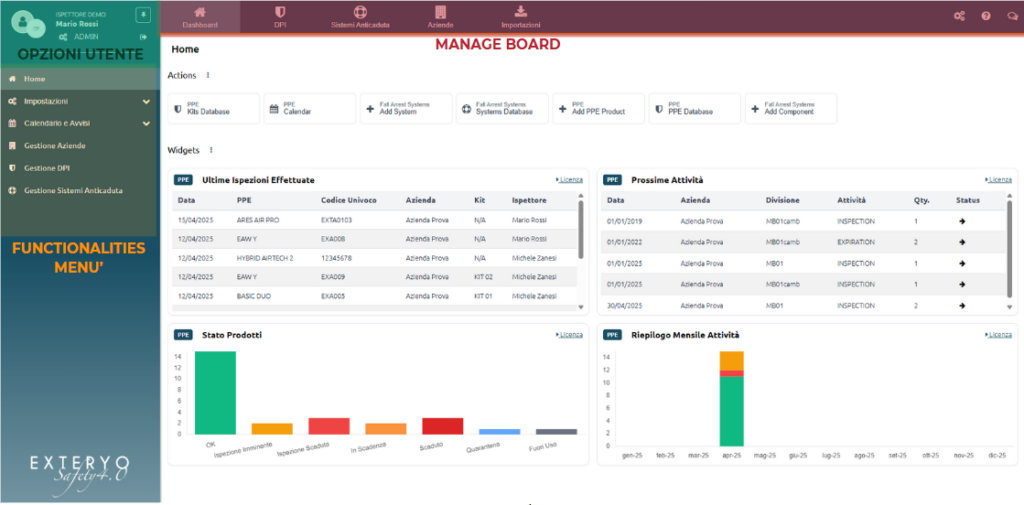
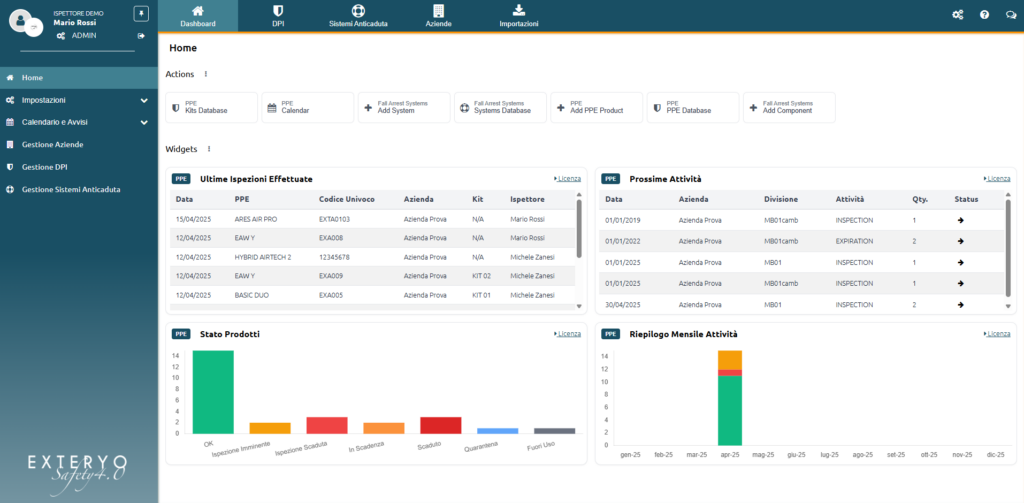
3.2 DASHBOARD
The Dashboard is the first page of access within the platform and allows you to find your way around the different functions in the system.
Through the Dashboard’s side menu, you can have immediate access to the main areas of use of the platform, while within the HOME function you can set the ACTIONS and WIDGETS needed to have a better experience of using the platform.
To learn how to set ACTIONS and WIDGETS, please read the next chapter
3.3 ACTIONS E WIDGETS
Actions and Widgets are platform tools that help you improve your experience of using the platform.
These tools are available both within the DASHBOARD section and within the DEVICES and BUILDINGS sections.
ACTIONS:
ACTIONS are shortcut keys that can be set to speed up access to certain application features.
To select the desired ACTIONS, click on the button to display all available options.
Once you have located the desired option, simply drag it above the separator line.
Similarly, should you wish to remove one of the previously selected options, you can drag it below the separation line.
WIDGETS:
WIDGETS are graphs supporting your activity as an INSPECTOR that allow you to view the following types of activity:
– Last Inspections performed
– Upcoming Calendar Activities
– Status of managed products
– Summary of activities performed month by month.
To select the desired WIDGETS, click on the button to display all available options.
Once you have located the desired option, simply drag it above the separation line.
Similarly, should you wish to remove a previously selected option, you can drag it below the separation line.
Within the DASHBOARD section, it is possible to display for each widget the activities related to both PPE and DASHBOARD SYSTEMS.
To change the display from PPE to Fall Protection Systems you can click on the BLUE button to the left of the widget description.
In all Sections you can view data on the general activity of the licence or of the individual inspector.
To change the view from LICENCE to USER, simply click on the appropriate button to the right of the individual WIDGET description.
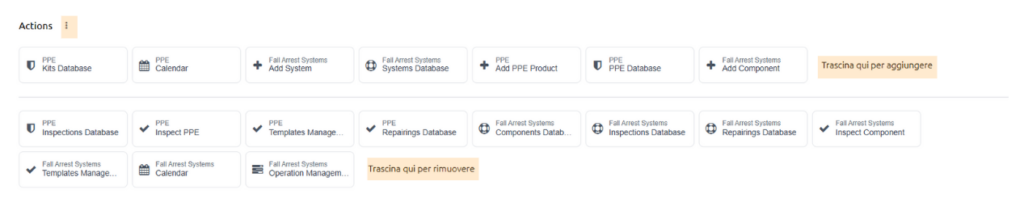
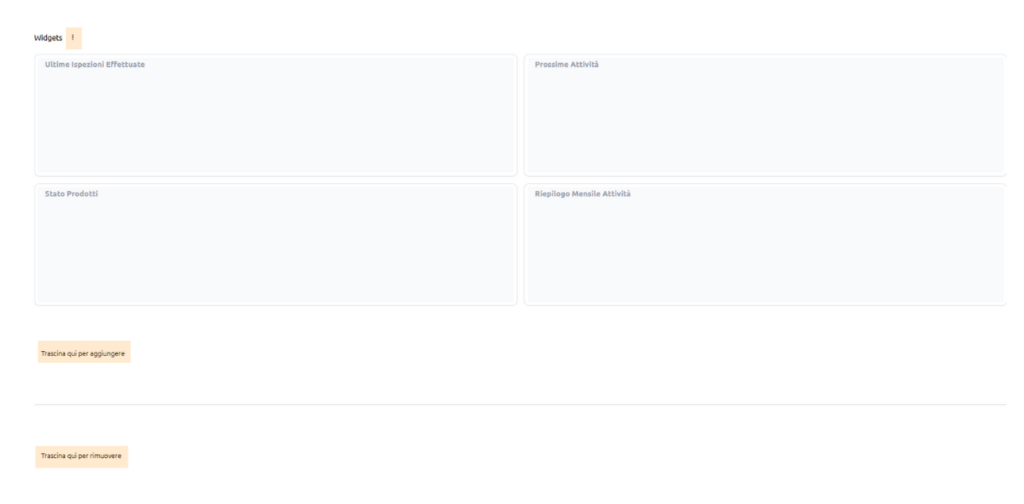
4. GENERAL SETTINGS
By clicking on the button on the right-hand side of the TOP MENU, you can access the GENERAL SETTINGS of your platform.
Within this menu there are various options which will allow you to customise and manage your activity with Exteryo Safety 4.0.
Let us see below the different options within the general settings.
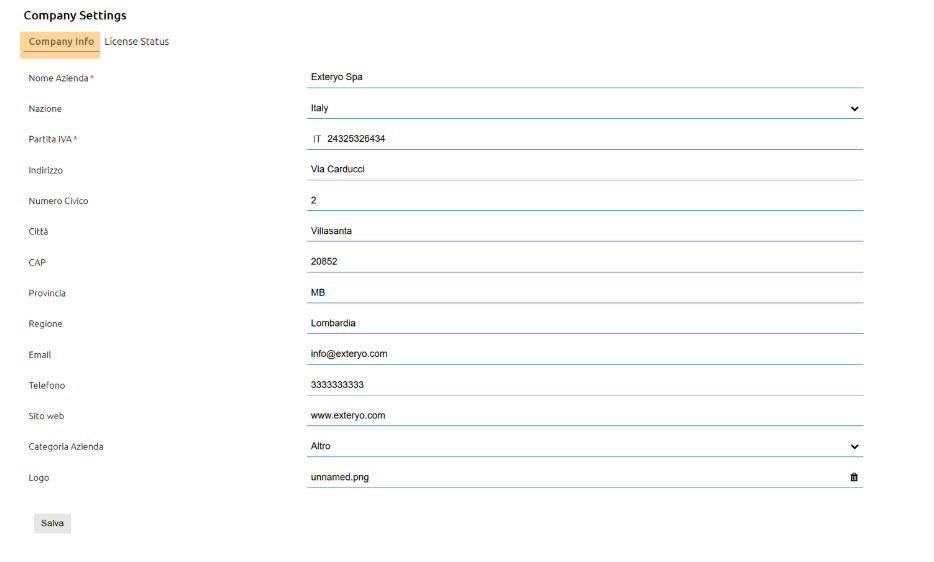

4.1 COMPANY SETTINGS (COMPANY DATA AND LICENCE STATUS)
Within the company settings you have the option of managing your company master data and licence status for ES4.0.
The first item that can be displayed is the COMPANY DATA item where you can view and manage the different information items.
Within the management items, you can also upload an image of your company logo if you have purchased the appropriate option.
Once the logo has been uploaded, it will be displayed within the PDFs of the downloaded inspection reports.
By scrolling through the horizontal menu of COMPANY SETTINGS, it is possible to access the LICENCE STATUS section to check the purchased software licence plan and the date of expiry or possible renewal.
4.2 ROLES AND USERS
In the ROLES AND USERS section, it is first of all possible to set privilege and display rules for definable activities for groups of users and workers within the platform.
This activity can be managed within the ROLES section.
When you activate your licence, you will already have several pre-configured roles within the table to which you can associate different users and workers.
You can change the management options for these roles at any time by clicking on the button and then the MODIFY ROLE entry.
Within the specific functionality you will find the possibility to edit the following information:
NAME: Defines the name given to the specific role
Hierarchical LIMIT: Defines the possibility for users and workers associated with that role to be able to view data on all company divisions (if the option ‘NO’ is indicated) or only divisions belonging to their own hierarchical branch (if the option ‘YES’ is indicated).
GERARCHIC ROLE: Allows that specific role to be associated with a role in the employer chain provided for by the safety regulations (Employer, Delegated Manager, Sub-delegated Manager, Supervisor or Worker).
DEPENDENT ON: Allows a relationship of dependence to be created in relation to another role.
PRIVILEGE MANAGEMENT: On the right-hand side of the page, it is possible for each type of activity to define whether or not a specific privilege is activated. For some functions, it is also possible to set the privilege only as a viewing option or as a data editing option.
Using the horizontal menu, you can also display the page dedicated to USERS.
All active users within the licence are displayed within this section.
Every worker Registryed within the platform is also automatically converted into a platform user by giving them the appropriate WORKER role.
It is possible for each user/worker within the table to change the associated role at any time as well as to decide whether to activate or block access to the platform.
Within the page it is also possible to create new users, assuming access to the platform even for profiles that are not employees of the company.
To create a new user, click the ADD USER button at the top right of the table and fill in the form with the required data.
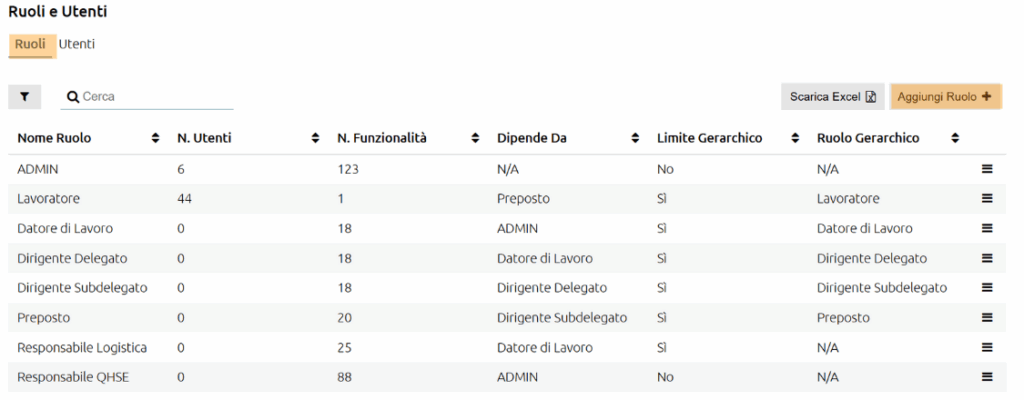
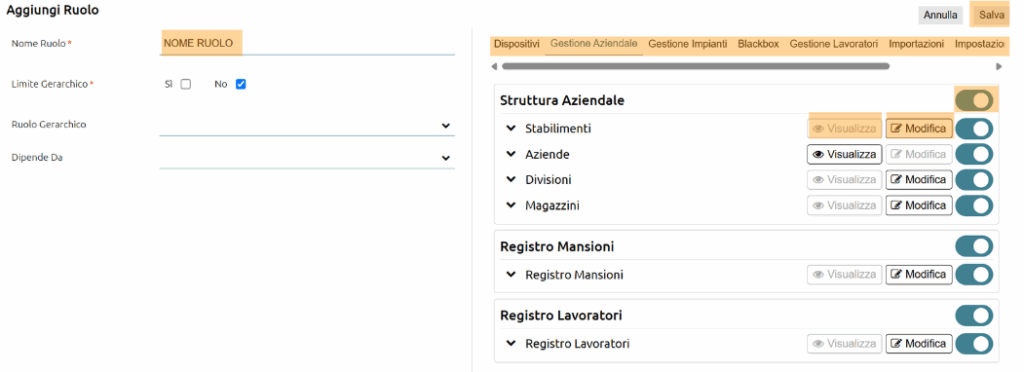
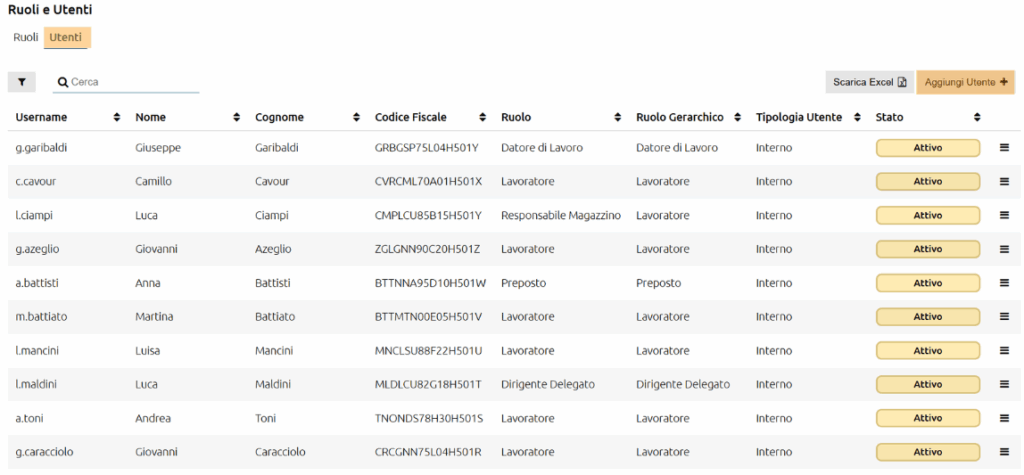
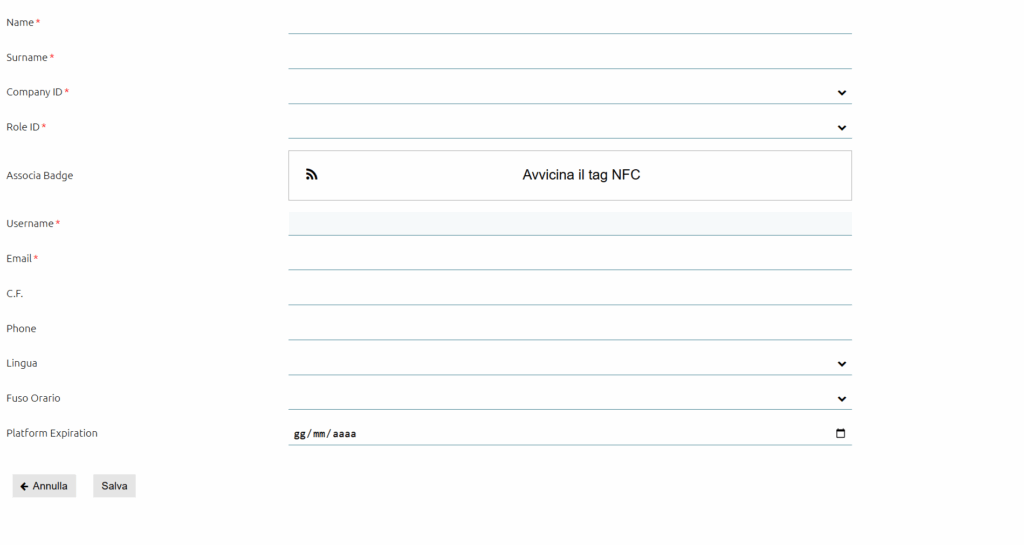
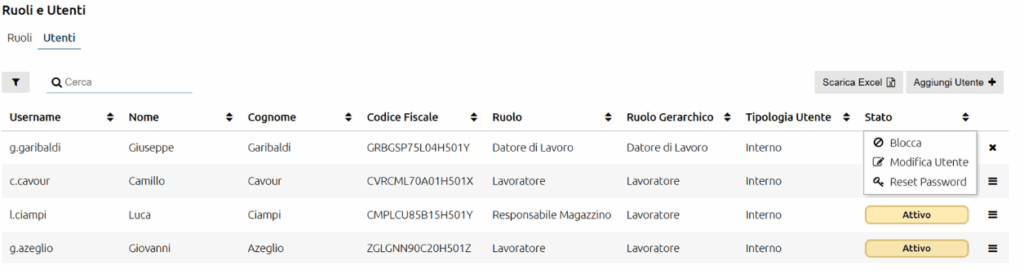

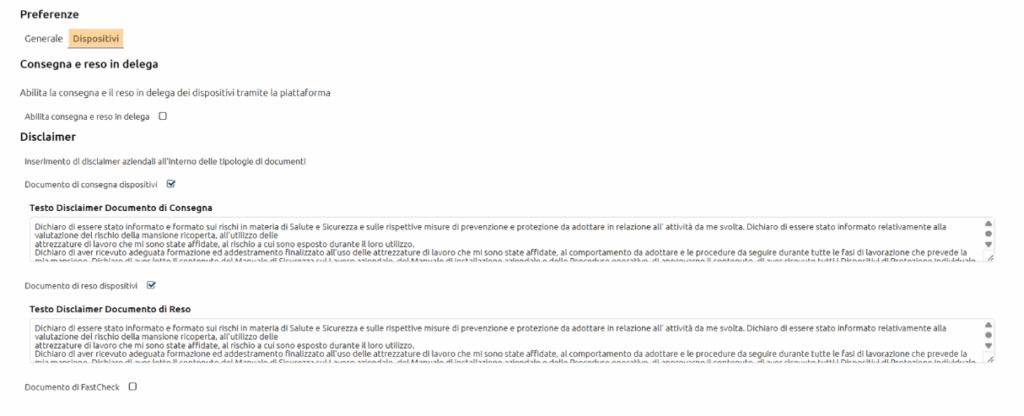
4.3 PREFERENCES
In the PREFERENCES section, you can manage any customisations and preferences for using the platform in different areas.
The function is divided into two macro-groups:
(i) GENERAL:
Allows the definition of general activities provided by the platform.
Inside, there is a preference concerning the SIGNATURE OF DOCUMENTS which can be set according to one of the following options:
Badge Signature: an electronic signature is provided by passing the badge and indicating the unique code of the NFC chip, the first name, surname and serial number of the employee owning the badge.
Calligraphic Signature: provides for the insertion of a calligraphic signature in electronic mode, which can be entered using the cursor on the PC or a special stylus on the smartphone screen.
Calligraphic Signature and Badge: this first involves the insertion of the calligraphic signature and subsequent validation by badge.
(ii) DEVICES
Allows the definition of preferences dedicated to device-related activity.
The first preference provided relates to the insertion of any DISCLAIMER in supply, return or delegated supply documents.
By activating one of the above options, it is possible to insert a text field that will be displayed in the appropriate documents.
The second preference option relating to devices concerns the MANAGEMENT OF DEVICES IN THE WAREHOUSE.
By enabling or disabling this option, it is possible to decide whether or not to take advantage of the warehouse control functions provided by the platform.
By enabling this option, in fact, it will be possible to create warehouses and manage the inventory and quantity control of each individual warehouse within the various warehouses.
If, on the other hand, the option is not enabled, the platform provides for the presence of a single fictitious stock without the possibility of checking the stock quantities of individual devices.
4.4 EXTERNAL MANAGEMENT
In this option it is possible to manage the synchronisation with any inspectors dedicated to inspecting company PPE or company fall protection systems.
There are two tables for both PPE and fall protection systems, one for licensed inspectors and one for inspectors who applied for a licence for at least one division or building.
When an inspector is synchronised with the company, data on devices, workers or buildings and components are shared within the inspector’s licence.
By clicking the button at the end of the row of one of the active inspectors, it is possible to manage the sharing mode, i.e. to define the DIVISIONS (or buildings) for which the inspector is authorised to manage the inspection activities.
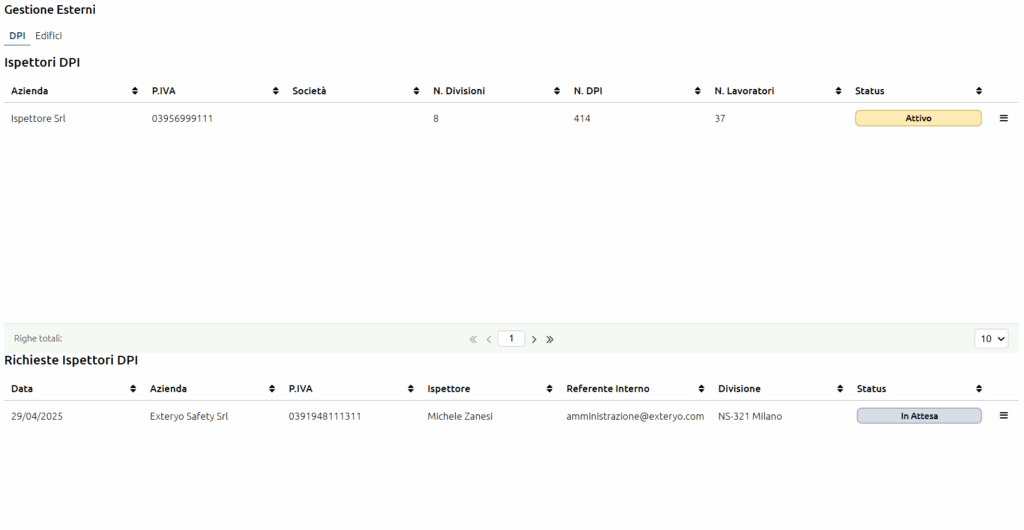


5. USER OPTIONS AND SUPPORT FUNCTIONS
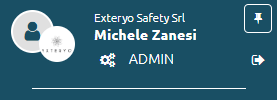
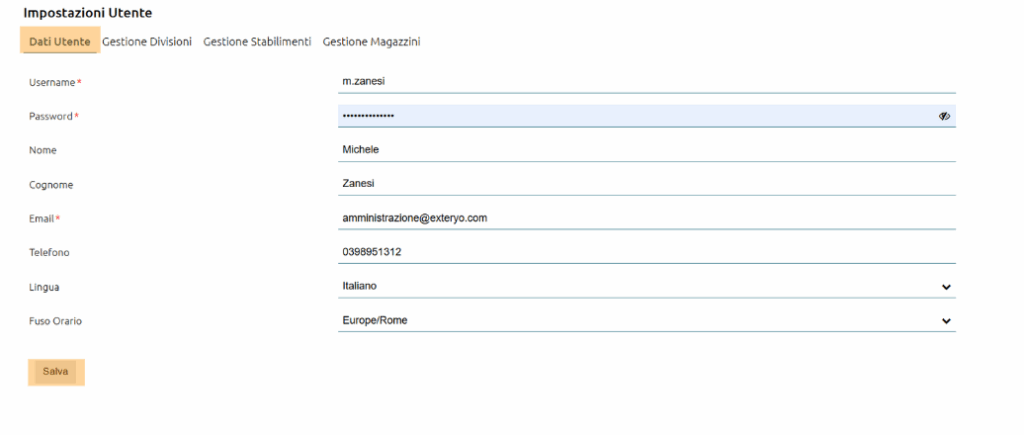
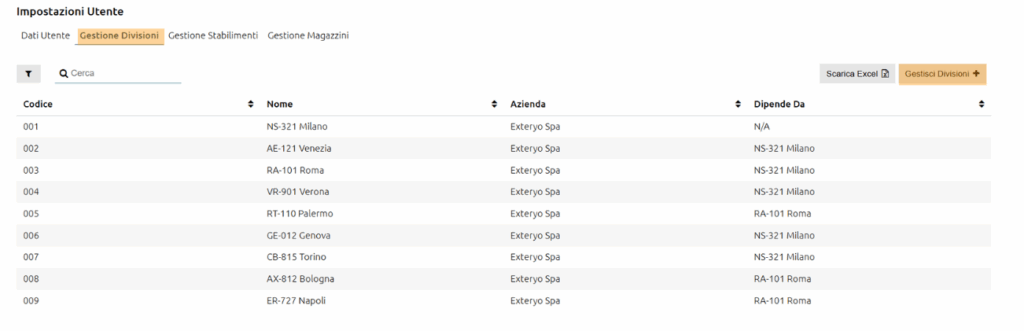
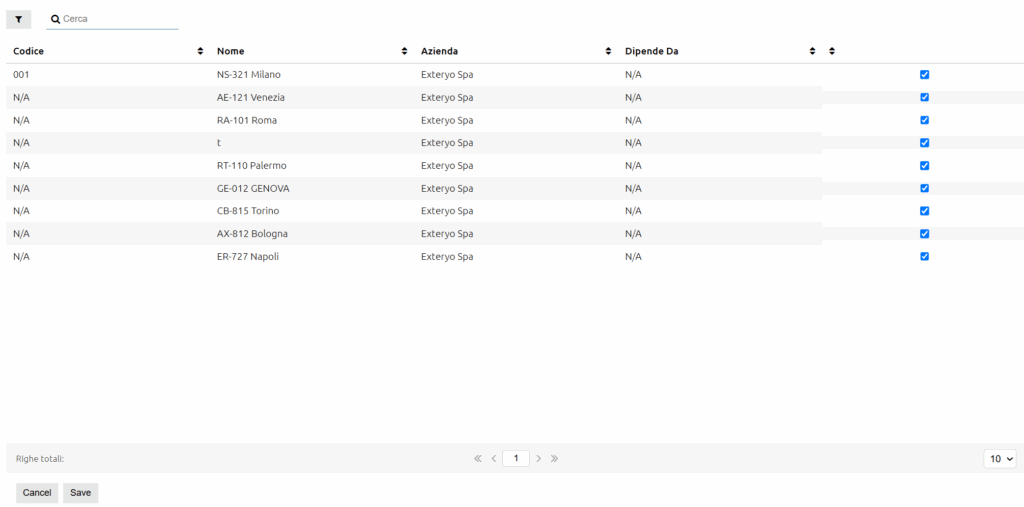
5.1 USER OPTIONS
The USER OPTIONS function allows you to customise your specific user data.
To access the function, click the button at the top of the SIDE MENU.
Within the USER DATA you can change some of your personal details such as your password, time zone or the language in which you use the platform.
In the DIVISION MANAGEMENT section you can define the divisions (and thus the respective workers and devices) you wish to have under your management.
You can add or remove divisions by clicking on the DIVISION MANAGEMENT button and selecting the flag to the right of each division.
In this table you will only see divisions available to you according to the role held and the hierarchical limit set.
To learn how to manage the hierarchical limits of divisions, please read section 4.2 ROLES AND USERS.
In the ESTABLISHMENT MANAGEMENT section, you can define the establishments (and thus the relevant facilities and fall protection systems) that you wish to have under your management.
You can add or remove establishments by clicking on the ESTABLISHMENT MANAGEMENT button and selecting the flag to the right of each establishment.
Only those establishments available to you will be shown in this table according to the role held and the hierarchical limit set.
In the STORE MANAGEMENT section, you can define which warehouses you wish to have under your management.
You can add or remove warehouses by clicking on the WAREHOUSE MANAGEMENT button and selecting or not selecting the flag to the right of each individual warehouse.
This table will only show the warehouses available to you according to the role you hold and the hierarchical limit set.
5.2 ACCESSING THE TUTORIAL
You can access the online version of this tutorial directly from the platform by clicking the button on the right-hand side of the TOP BAR.
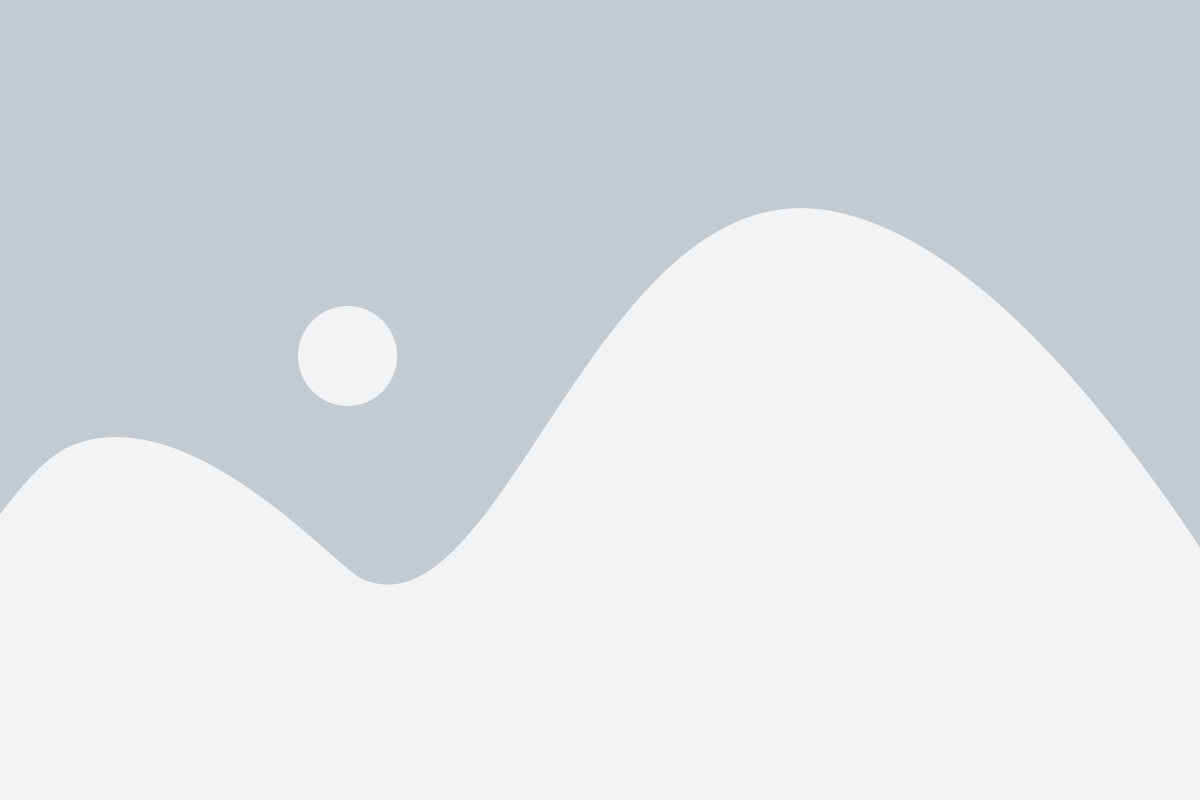
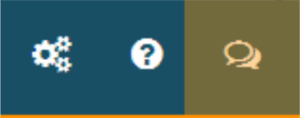
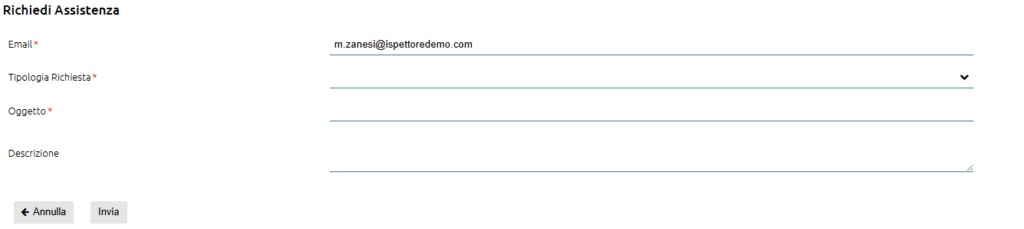
5.3 GET ASSISTANCE
Should you not find the appropriate answers within this tutorial, you can always open a support ticket within the specific function.
To access the function, click the button on the right-hand side of the TOP BAR.
Within the window, fill in the form indicating the e-mail address on which you would like to receive a reply to your request, the type of request (technical or commercial) and then the subject and description of the request.
Our Customer Care service will receive and handle your request as soon as possible. Please note that the service is active from Monday to Friday from 9:00 a.m. to 6:00 p.m. (Central European Time- CET) and responds to requests within 4 hours of receipt.
6. ITEMS MANAGEMENT
6.1 ITEMS - HOME
The ITEMS section groups together all the functions that allow you, according to the privileges provided by your role, to control and manage the PPE, workwear or any kits supplied to company workers or present in the warehouse
In the HOME function of the IPR section you can set up ACTIONS and WIDGETS to support your activity.
To learn how to manage these tools, please read the appropriate section of the ACTIONS AND WIDGETS tutorial.
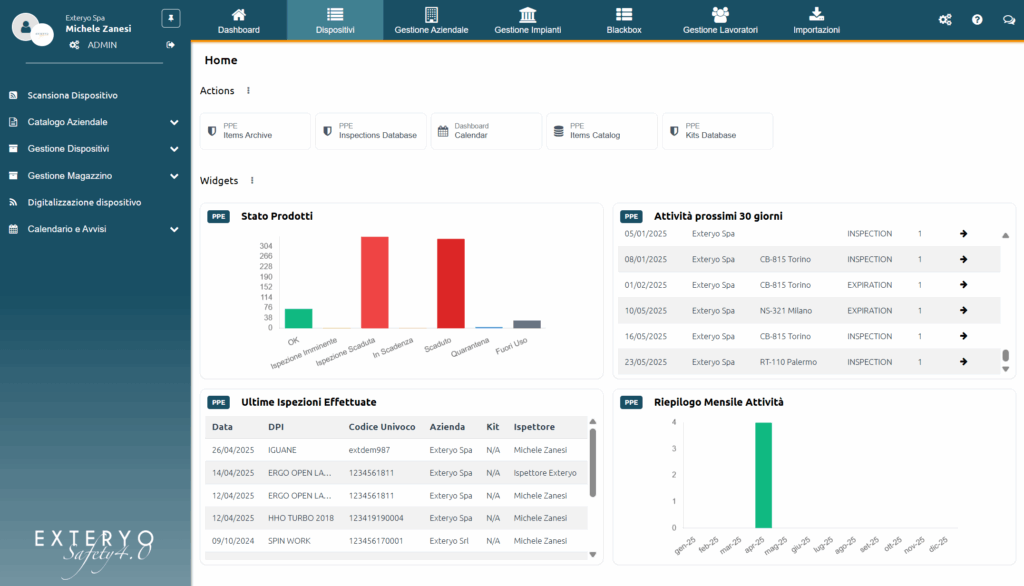
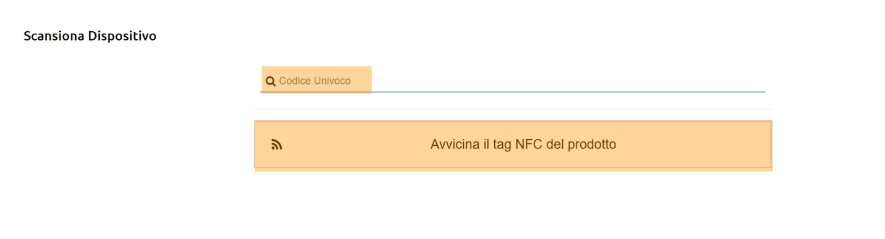
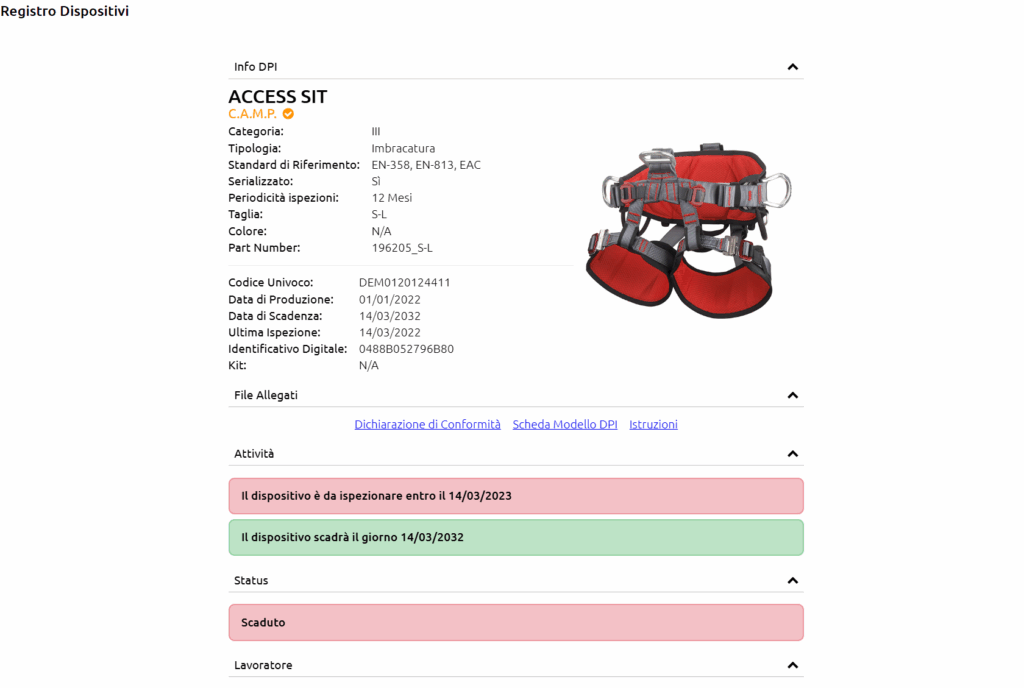
6.2 ITEMS – SCAN ITEM
The SCAN ITEM function allows you to access the specific product data sheet of a PPE, an item of workwear or a KIT managed by you, by reading the appropriate digital identifier (NFC/Qrcode) or by manually entering the product’s unique code.
This function is only available for SERIALISED devices, i.e. with a unique code and possibly a digital identifier (NFC, Qrcode).
Unlike the OPEN PRODUCT SHEET function on the Log-in page, the SCAN ITEM function gives you access to all product data, including company and associated worker data.
6.3 ITEMS – UNIFORM GROUPS
Within the COMPANY CATALOGUE menu, the function UNIFORM GROUPS allows you to create identification groups for PPE or Workwear for specific Device models.
This functionality allows first of all to group different PPE or workwear models into a single management group, but above all to set certain rules concerning the supply and return of devices.
When a new uniform group is added, in addition to the code, name and a possible description, an indication is requested as to whether the specific uniform code will provide for the management of CONSUMABLE Devices or not.
Within the platform, a device without a unique identifier and with a high level of replacement (e.g. a pair of gloves or a pair of shoes) is defined as a CONSUMABLE.
If YES is selected under consumable, all PPE models that will be associated with that uniform group will be replaced at the time of a new supply without the need for a return.
If, on the other hand, NO is selected under consumable, it means that the models associated with that uniform group will have a unique recognition and therefore each device will have to be provided with its own serial code and possibly a digital identifier (NFC/Qrcode).
This means that the code of the device supplied will have to be specified in detail at the delivery stage and this will provide for a return to stock at the end of activity or end of life.
Furthermore, if NO is selected in the CONSUMABLE option, it must be specified whether devices belonging to that uniform group require inspection or not.
.
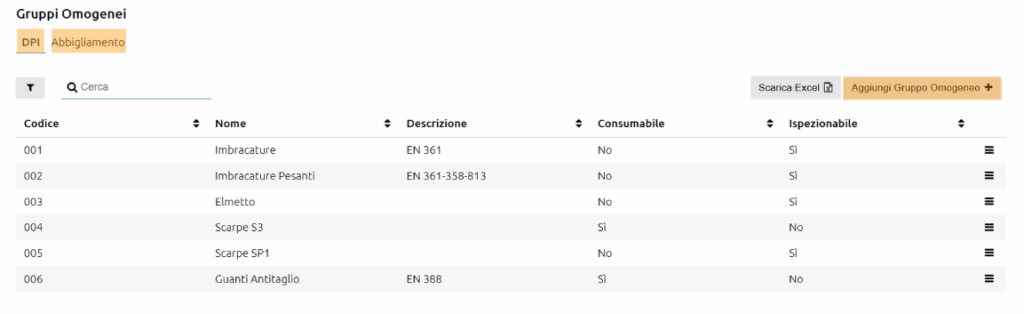
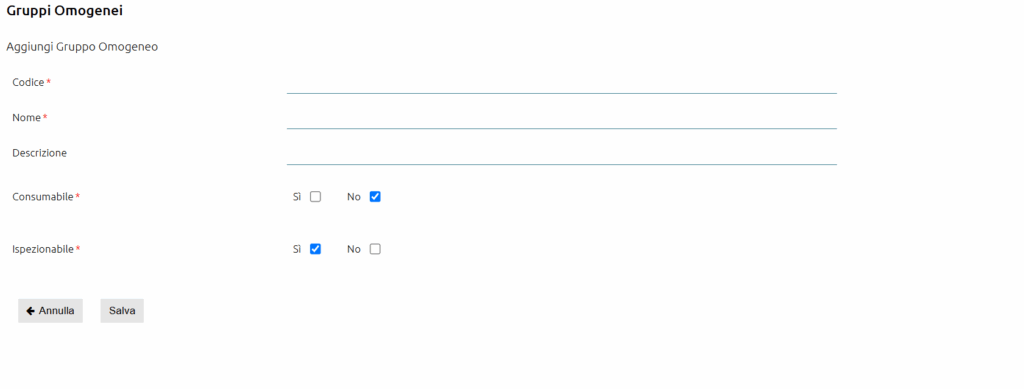
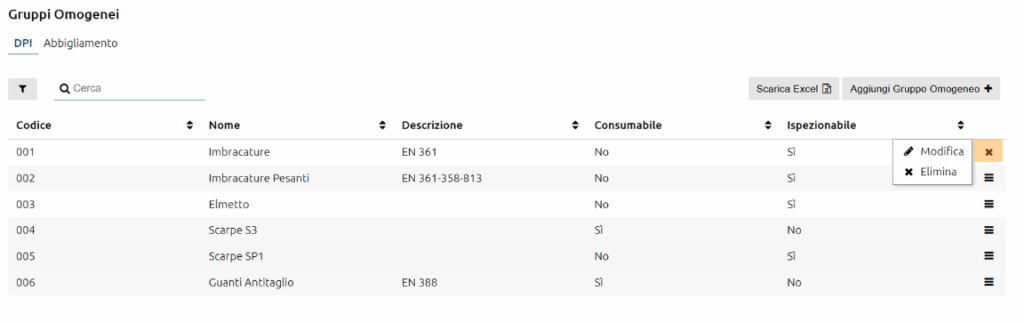
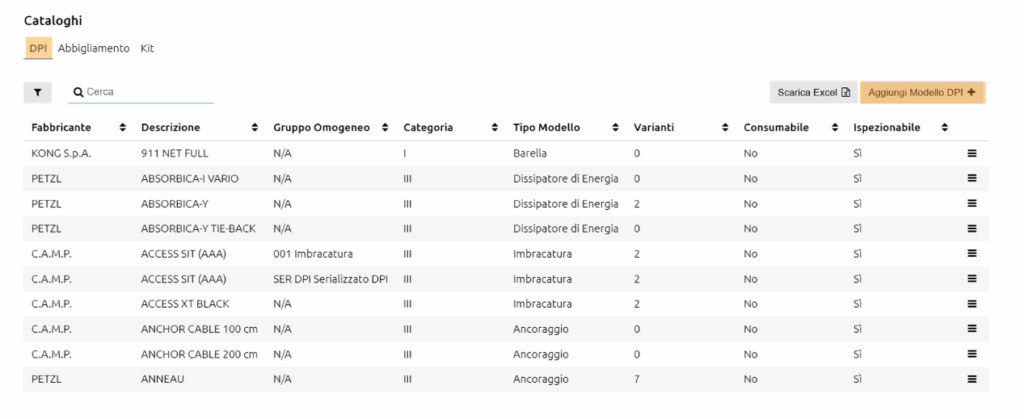
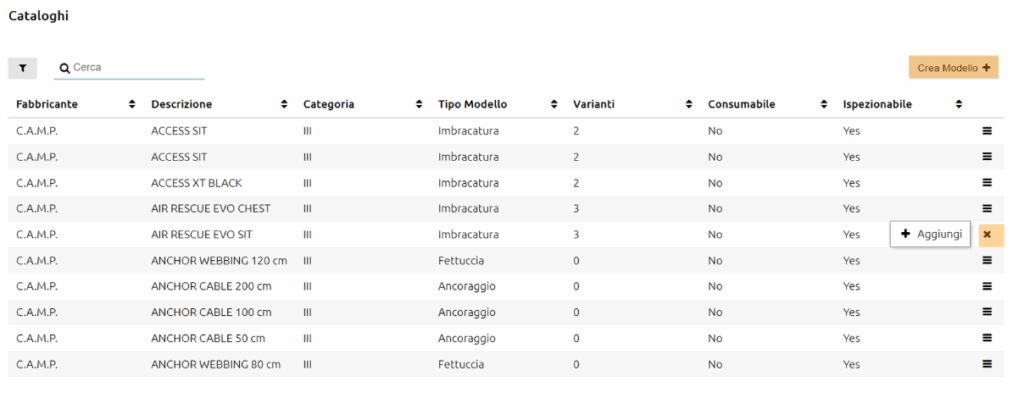
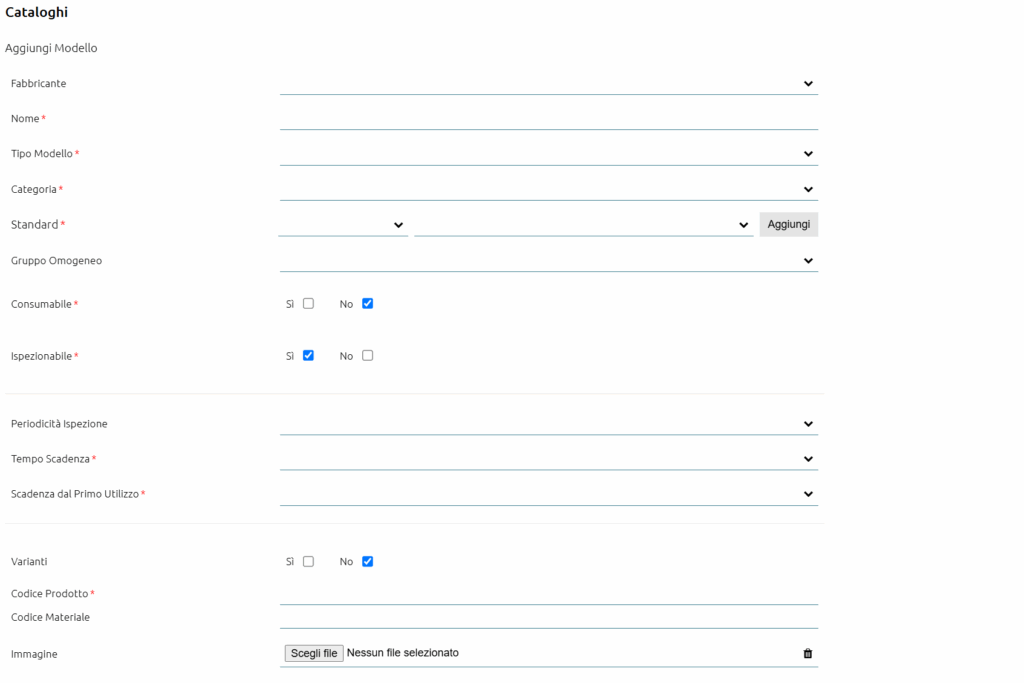
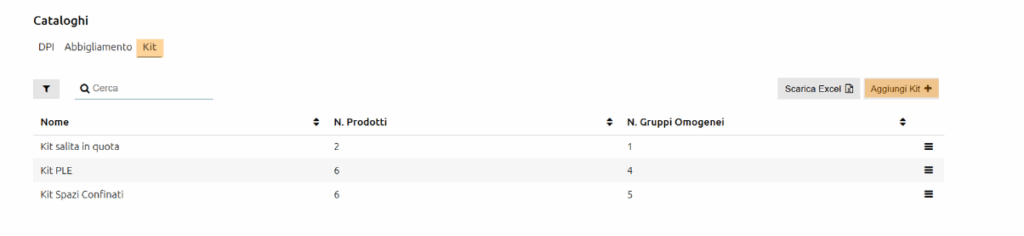
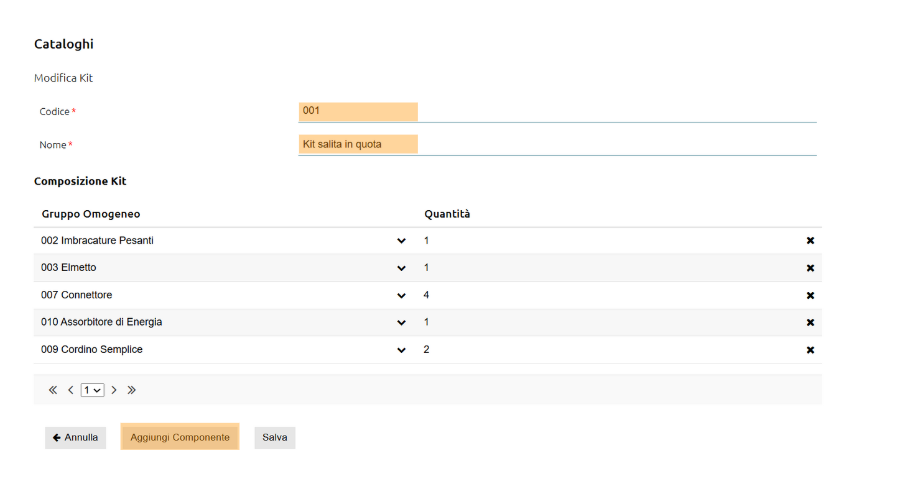
6.4 ITEMS – CATALOGUES
Within this function, it is possible to generate company catalogues dedicated to PPE, workwear and any types of KIT managed by the company.
Let’s take a detailed look at the three different types of catalogue and their options.
PPE CATALOGUE
This allows you to create and manage information on the different PPE models managed in your company.
To add a new PPE model, click on the ADD PPE MODEL button at the top of the table. The page that opens will show the database of PPE models already pre-provided by the platform, whose sheets have been entered directly by the PPE manufacturers.
If the model you need is among those in this database, simply click the button and select ADD.
Once this action has been taken, the tab of the model you wish to add will open, to which you can possibly change the name, enter a homogeneous reference group and any MATERIAL CODES (internal company code) for each specific variant of that model.
If, on the other hand, the PPE model to be added to the catalogue does not exist in our general database, you can create it by clicking on the CREATE TEMPLATE button.
This will open the form for entering the data required to create the PPE model.
WORKWEAR CATALOGUE
It allows you to create and manage information on the different garment models managed in your company.
To add a new garment model, click on the ADD WORKWEAR button at the top right of the table.
This will open the form for entering the data required to create the garment model.
KIT CATALOGUE
Allows the creation of organised KIT templates used within the company.
To add a new KIT model, click on the ADD KIT button and enter a specific coding and the name of the relevant model.
It is then possible to compose the kit by adding the different components using the ADD COMPONENT button.
For each component inserted, the specific uniform code and the relative quantities must be indicated.
6.5 ITEMS – ITEMS REGISTRY
This function, found within the ITEMS MANAGEMENT menu, allows the management of all company devices, divided into PPE and workwear, to be kept under control.
Once a catalogue model has been generated, it will also be displayed within the Item Registry with an indication of the status of each individual device, diversified between “In use”, “in Warehouse”, “in quarantine” or “Out of use”.
By clicking on the button placed at the end of the line of a specific model and then clicking on the SHOW ITEMS button, it is possible to access precise information on each individual device in use and diversified between the various statuses.
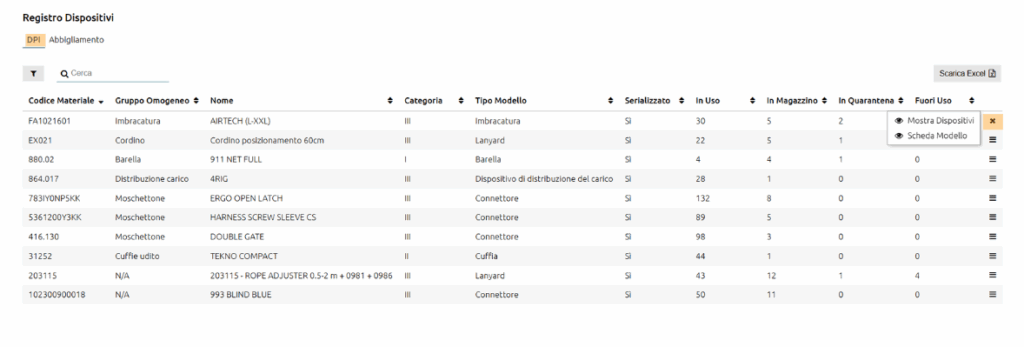

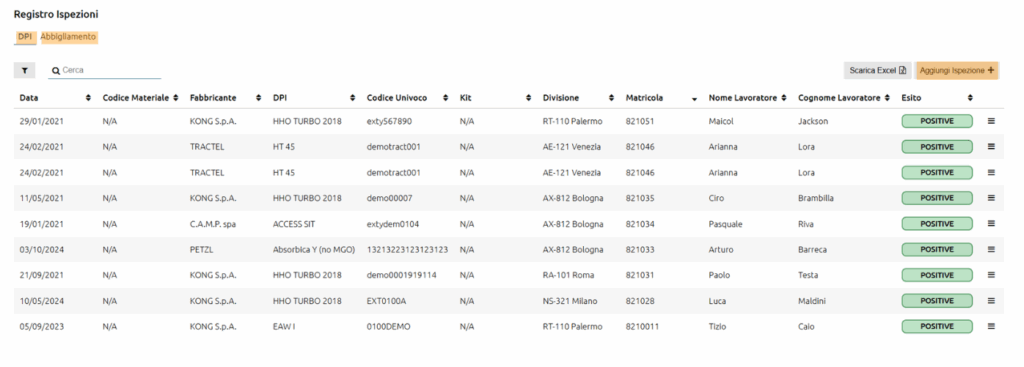
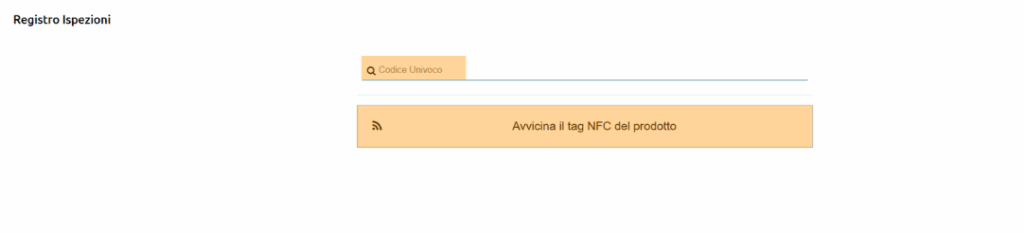
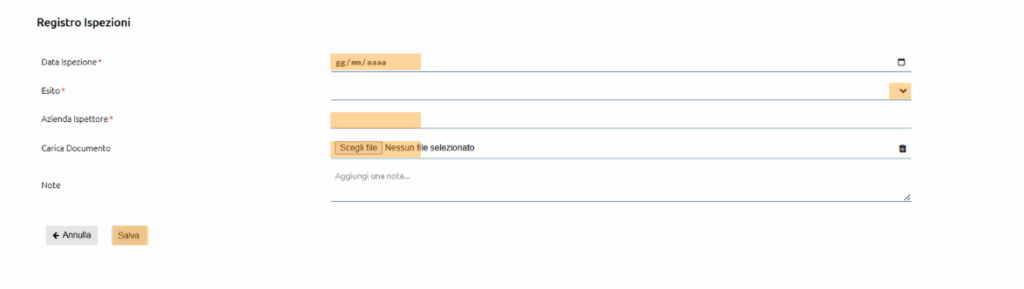
6.6 ITEMS – INSPECTIONS REGISTRY
Inspections of company devices will be displayed in this table.
Inspections can be managed by an external inspector using his dedicated Exteryo Safety 4.0 licence.
By clicking on the button, it will be possible to view the relevant inspection sheet or download a PDF of it.
It is also possible to add repairs manually by clicking the ADD INSPECTION button and entering the unique product code (or reading the digital identifier).
Then simply enter the data requested in the form and attach the inspection document.
6.7 ITEMS – REPAIRS REGISTRY
In this table, repairs to company devices can be viewed.
Repairs can be managed by an external inspector via his dedicated Exteryo Safety 4.0 licence.
By clicking on the button, it will be possible to view the relevant repair record or download a PDF of it.
It is also possible to add repairs manually by clicking the ADD REPAIR button and entering the unique product code (or reading the digital identifier).
The system will only allow the management of those devices that have received a result TO BE REPAIRED in a previous inspection carried out.
Then simply enter the data requested in the form and attach the inspection document.
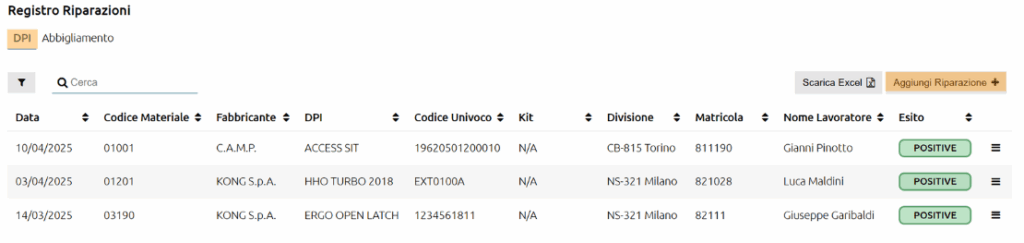
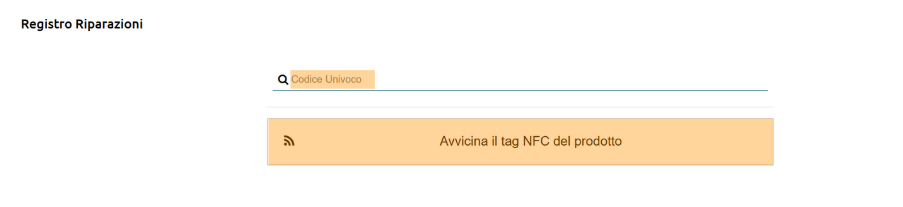
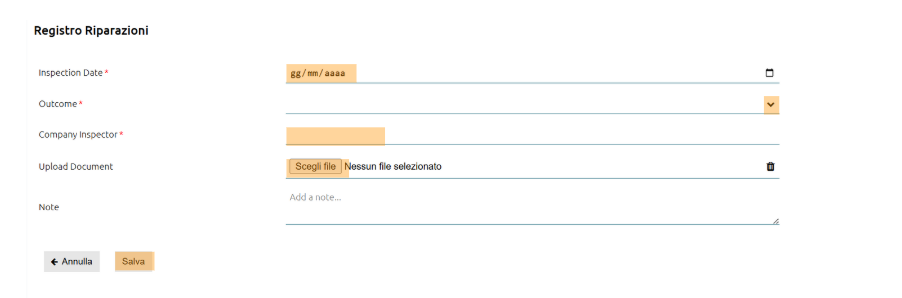
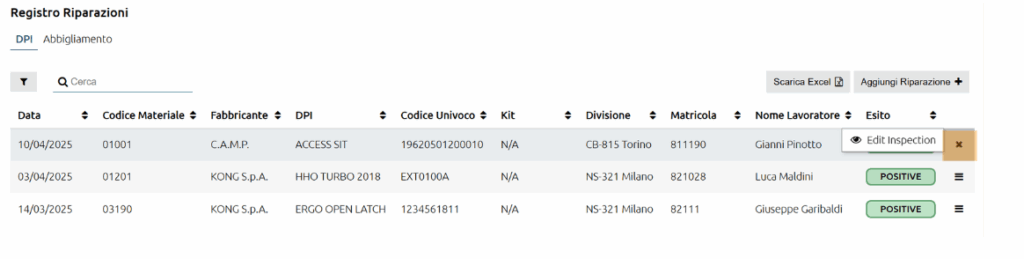
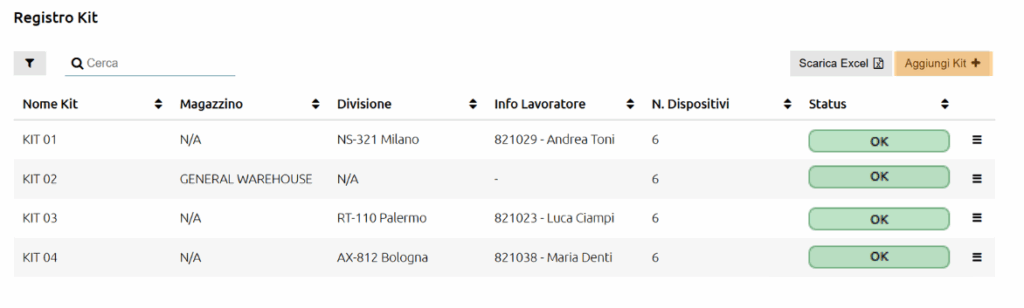
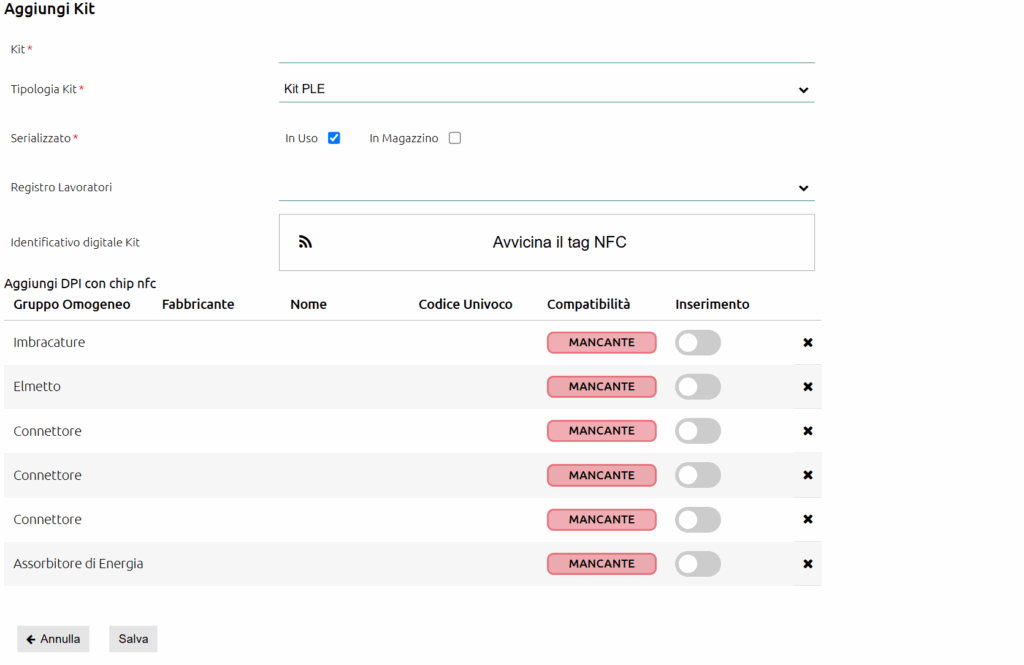
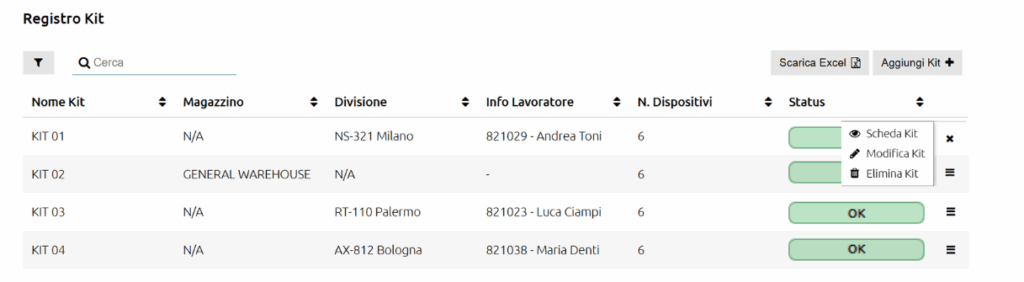
6.8 ITEMS – KIT MANAGEMENT
The KIT MANAGEMENT function allows the creation of specific Item Kits for company workers.
It is possible to generate a new kit by clicking the ADD KIT button at the top right of the table and then entering the required information such as Kit Name, Kit Type.
Subsequently, it is possible to indicate whether the Kit is already in the possession of a specific worker, or is in stock and finally it is possible to digitise the Kit by means of a specific digital identifier.
To add the specific PPE to the Kit, simply read the NFC chip associated with the PPE with your smartphone or a special reader
Depending on the Kit model selected, the system will show the missing PPE when the Kit is completed. It is however possible to create the Kit at one’s own discretion by inserting material of a different type or in a different number to that recommended by the Kit model.
6.9 ITEMS – SUPPLY
The Supply and Return functionalities, provided within the WAREHOUSE MANAGEMENT menu, allow the management of deliveries and eventual restocking of devices intended for workers.
The PPE supply firstly involves selecting the worker to whom the devices are to be supplied and, if applicable, the management warehouse (if warehouse management is enabled in PREFERENCES).
It is then possible to indicate whether the supply of the devices to the worker takes place DIRECTLY or BY DELEGATION.
If the delivery is made by DELEGATION, the employee delegated to collect from the warehouse must be indicated.
Then it is possible to select the PPE or workwear or kits to be delivered to the worker by means of the appropriate entries.
For each entry, you can select the device directly from the company catalogue entries, or by reading the appropriate Digital Identifier (only for non-consumable devices with a digital identifier).
Should the selection from the catalogue be chosen, to add the device click on the ADD button in the ACTION column and subsequently indicate the number of devices to be supplied.
If the supply concerns non-consumable PPE and/or with an expiry date, it will be necessary to enter the specific serial code, the possible date of manufacture and the possible digital identifier.
If the stock management option is activated, it is necessary to have the correct stock of that specific product in the warehouse, otherwise the add option will not be displayed.
Once all the required devices have been selected, which can be seen in the SELECTED DEVICES table, click on the SAVE button to proceed with the generation of the delivery report.
Within the generated delivery report, it is possible to add any notes in the provided field and to sign the document by the worker (or delegate) according to the signature mode defined within the preferences.
Once the signature has been entered, click on the SAVE button to complete the delivery of the devices.
In the case of a delivery in delegation, an additional document signature step is required on the part of the recipient worker.
For information on how to carry out this activity, please refer to the appropriate section “12.2 DELEGATED SUPPLY” in the worker access chapter.
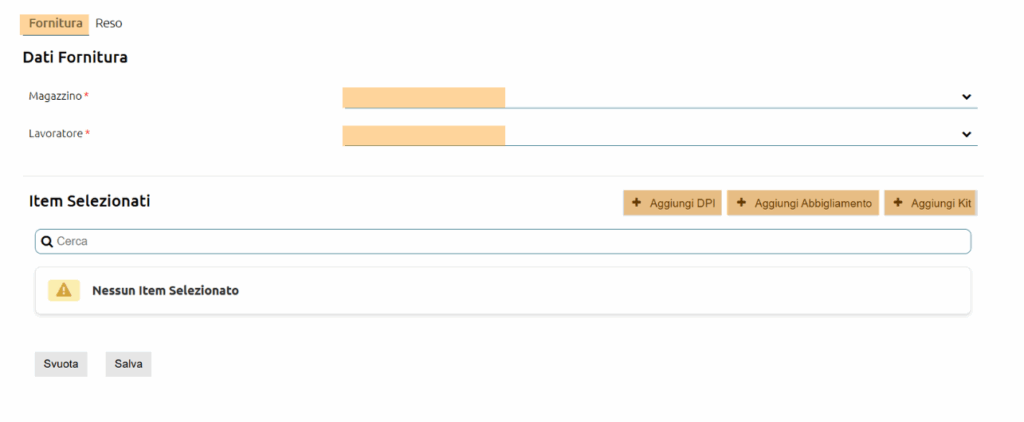
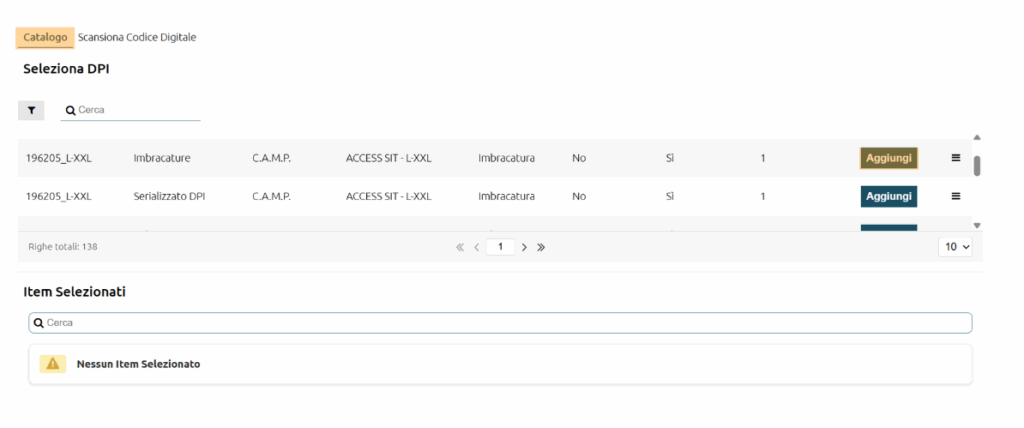
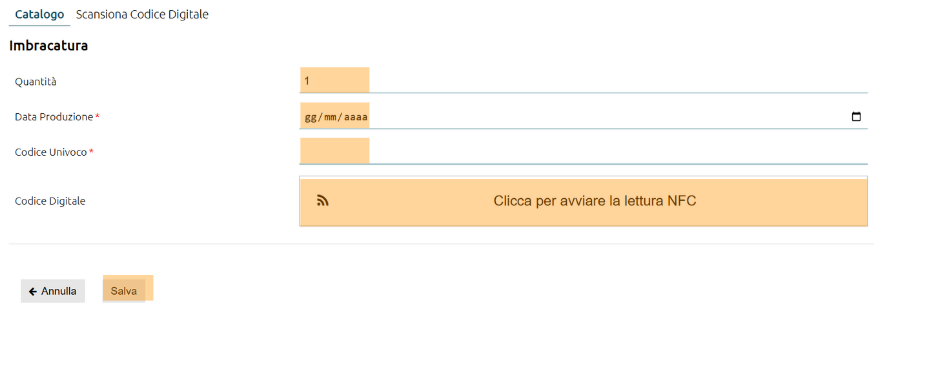
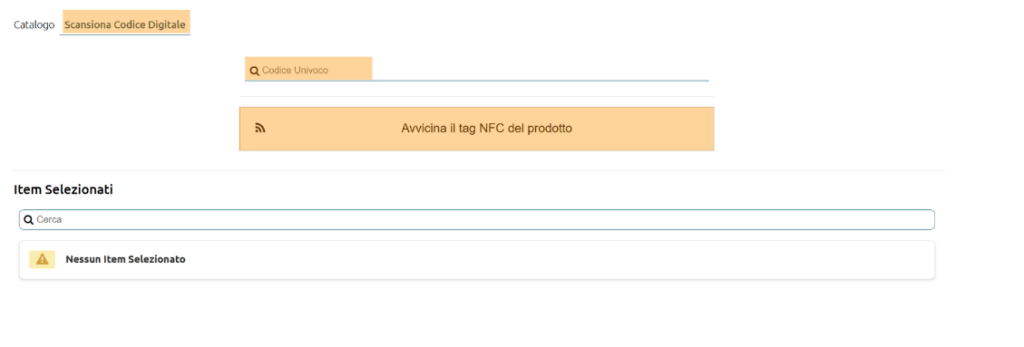
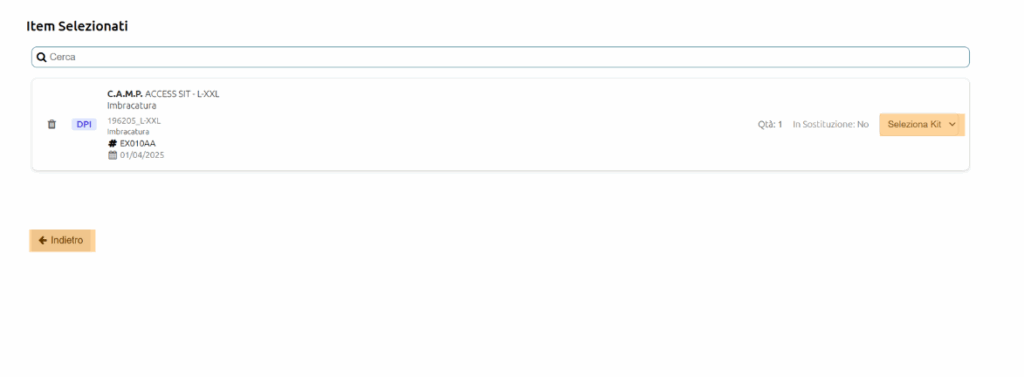
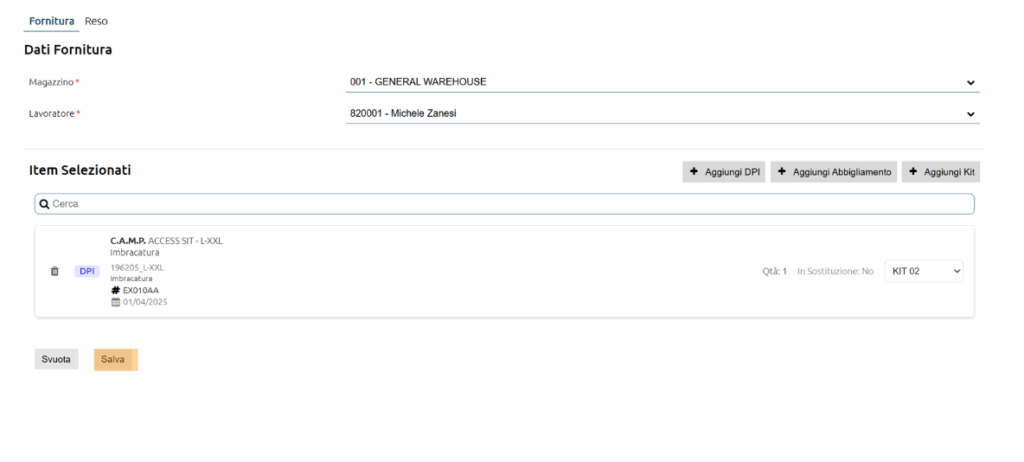
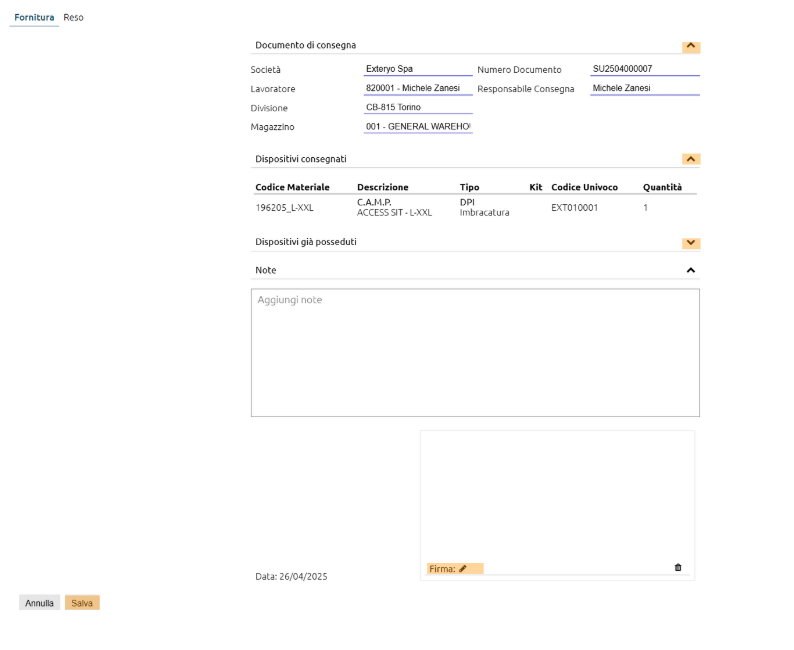
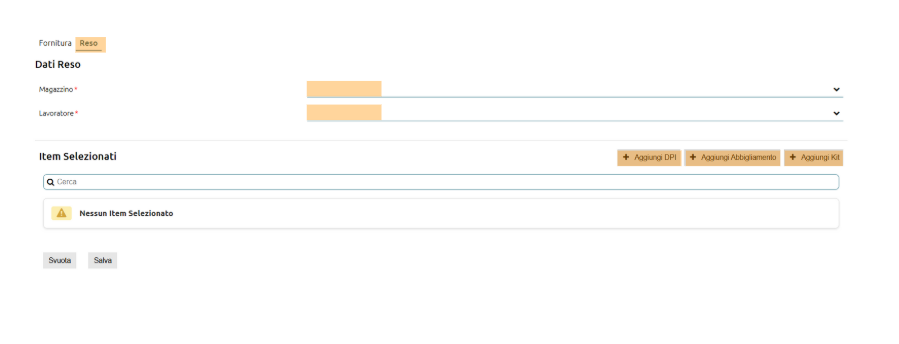
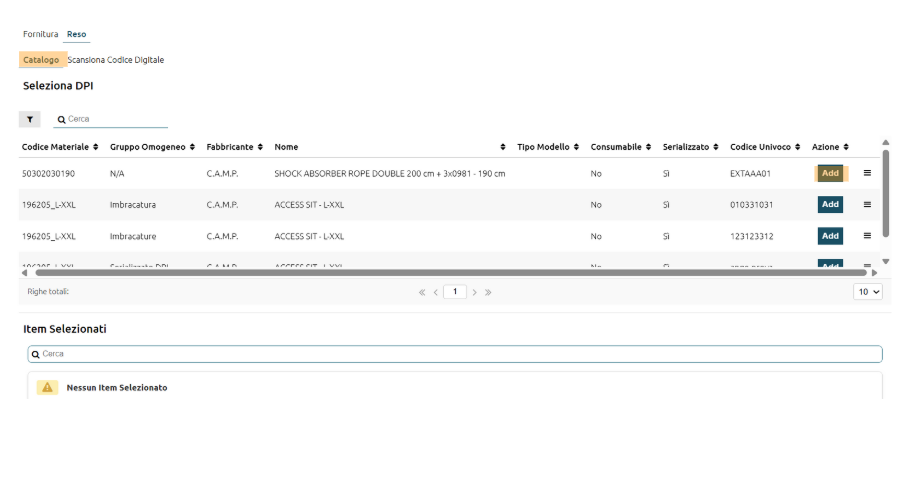
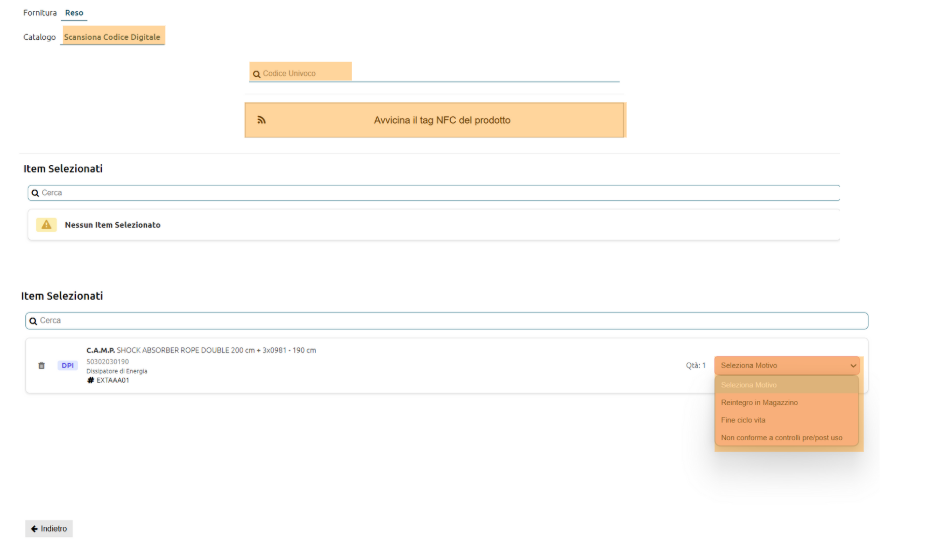
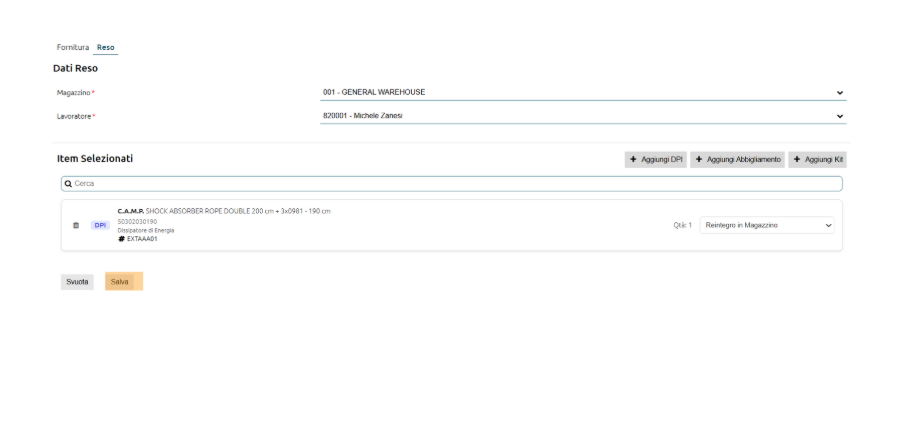
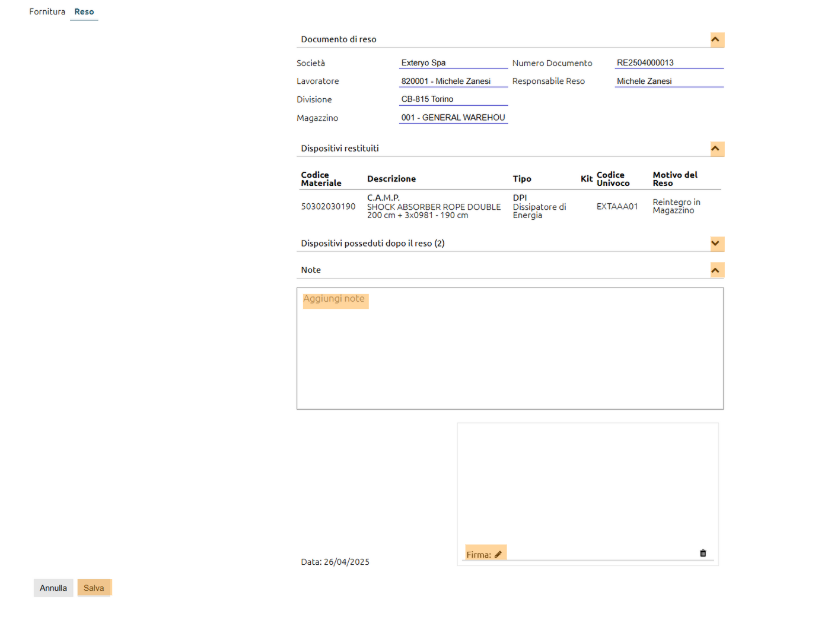
6.10 ITEMS – RETURN
The return activity, provided for within the function SUPPLY AND RETURN, allows the worker to return one or more devices from the NON CONSUMABLE to the warehouse.
To make a return, select the worker and, if necessary, the management warehouse (if warehouse management is enabled in PREFERENCES) in the appropriate function.
It is then possible to indicate whether the return of devices by the worker takes place DIRECTLY or BY DELEGATION.
If the return is made by DELEGATION, the employee delegated to return to the warehouse must be indicated.
Subsequently, it is possible to select the PPE or workwear or kits to be returned by the worker using the appropriate entries.
For each entry, it is possible to select the device directly from the worker’s device entries, or by reading the appropriate Digital Identifier (only for non-consumable devices with a digital identifier).
Should the selection be made from the list of available devices, to select the device click the ADD button in the ACTION column.
Once this has been done, the device in question will appear in the Selected Items column and the reason for returning the device must be selected from three different items in the drop-down menu:
– RETURN TO WAREHOUSE: in this case, the device is simply put back into storage without any change in its health status.
– END OF LIFE CYCLE: In this case the status of the PPE becomes ‘OUT OF USE’ and can no longer be supplied to another worker.
– NOT COMPLIANCE WITH PRE/POST USE CHECKS: In this case, the status of the PPE becomes ‘QUARANTINE’ and an inspection by a dedicated inspector will be required to return it to use.
Once all devices to be returned have been defined, click on the SAVE button to generate the return document.
Within the generated return report, it is possible to add any notes in the provided field and to sign the document by the worker (or delegate) according to the signature mode defined within the preferences.
Once the signature has been entered, click on the SAVE button to complete the return of the devices.
In the case of a proxy return, an additional document signature step is required on the part of the recipient employee.
For information on how to carry out this activity, please refer to the appropriate section on worker access.
6.11 ITEMS – INVENTORY
The INVENTORY function, which can be found within the WAREHOUSE MANAGEMENT menu, is only available if warehouse management has been enabled in PREFERENCES.
With this function it is possible to manage the stock quantities of the different device models within the individual warehouses.
By selecting the warehouse, it is first of all possible to view the quantities present for each individual device model.
By clicking the button at the end of the line of a specific model, and then selecting MANAGE INVENTORY, it is possible to access the management of quantities for each variant.
To increase or decrease the stock quantity of a specific variant, simply change the number in the ‘NON-DIGITALISED’ column and then click the CONFIRM button.
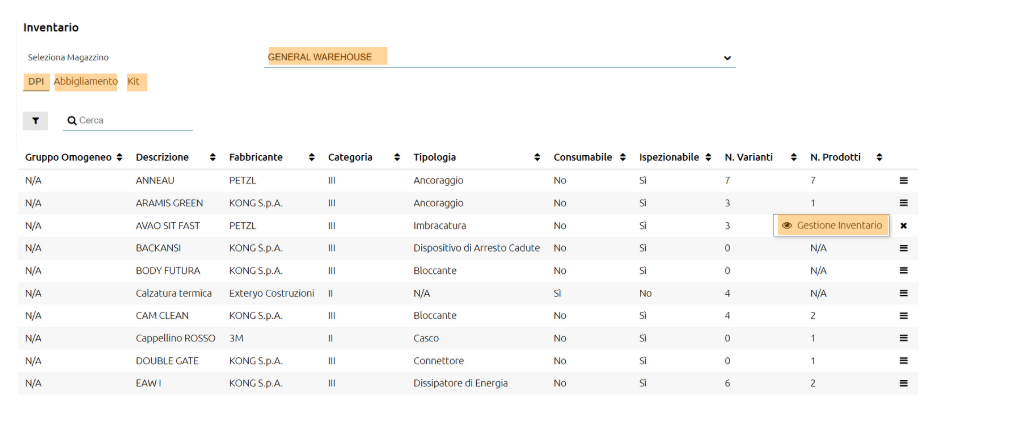
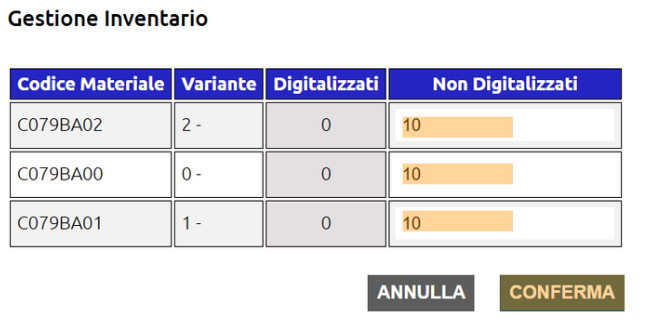
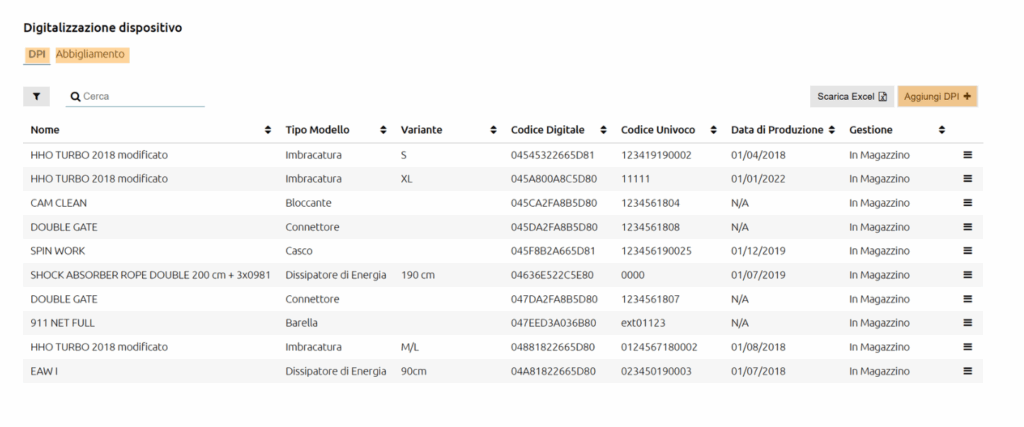
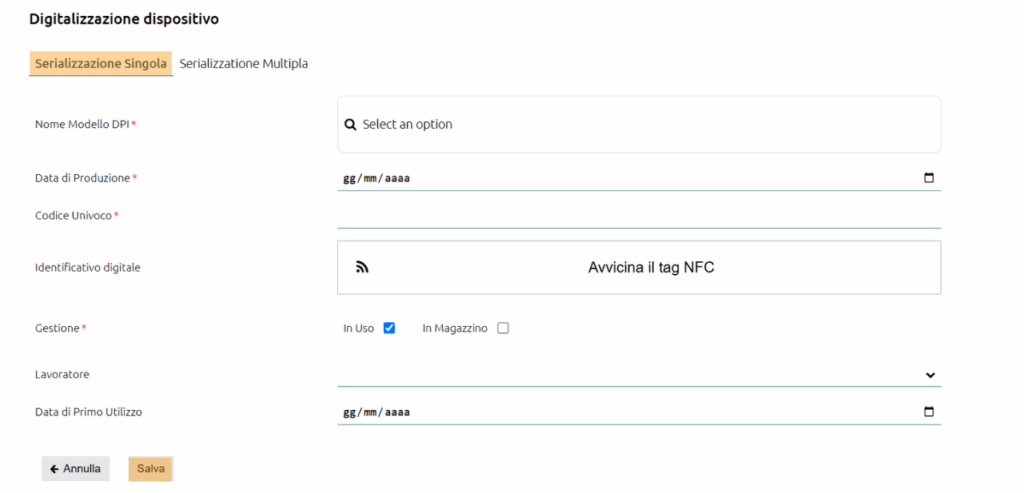
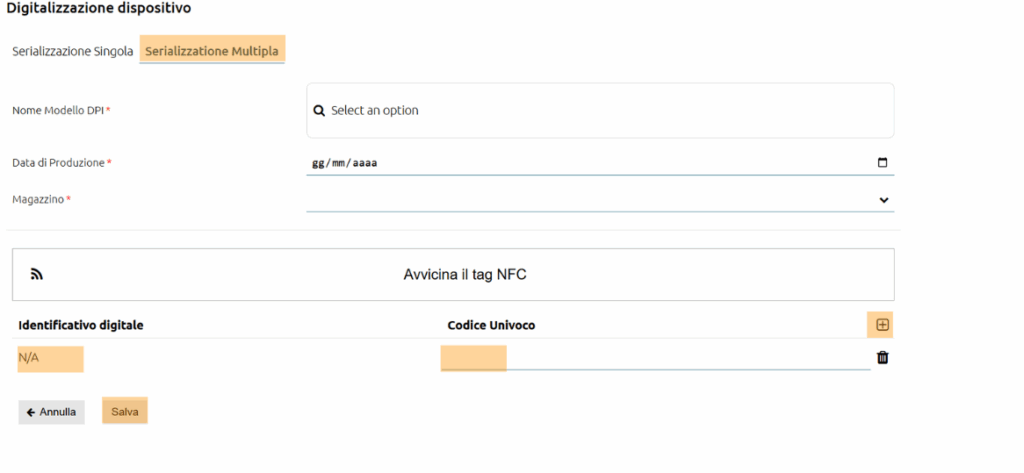
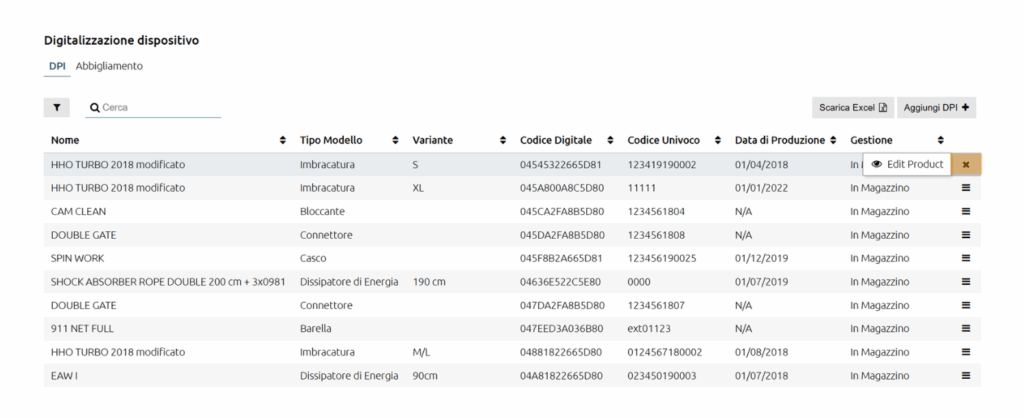
6.12 ITEMS – ITEMS DIGITALIZATION
This function makes it possible to manage all serialised devices managed by the company, by modifying any management data, such as model, production date, unique code, digital identifier or usage data.
This function can also be used to manage the digitization of new items in the company.
To carry out this activity, click on the button ADD PPE (or ADD WORKEWAR) and then choose between the option SINGLE SERIALIZATION or MULTIPLE SERIALIZATION.
In the case of Single Serialization, fill in the present form with the required data and finally click on the SAVE button to add it to the company management.
In the case of multiple serialization, first select the PPE model, production date and management warehouse (if warehouse management is enabled in PREFERENCES).
Then read the digital identifiers of the products to add them to the list and enter their unique codes.
If products do not have a digital identifier, they can be added manually by clicking the button and then adding the relevant unique code.
Once the entry is complete, click on SAVE to add the devices to the company management.
6.13 ITEMS - CALENDAR
Within the CALENDAR AND ALERTS menu you can access the CALENDAR function through which you can have a visual report of the different activities organised month by month.
By clicking on a specific notice in one of the calendar dates you will be directed to the EVENTS function already filtered for that specific day and that specific activity, so that you can get more details on the planned activity.
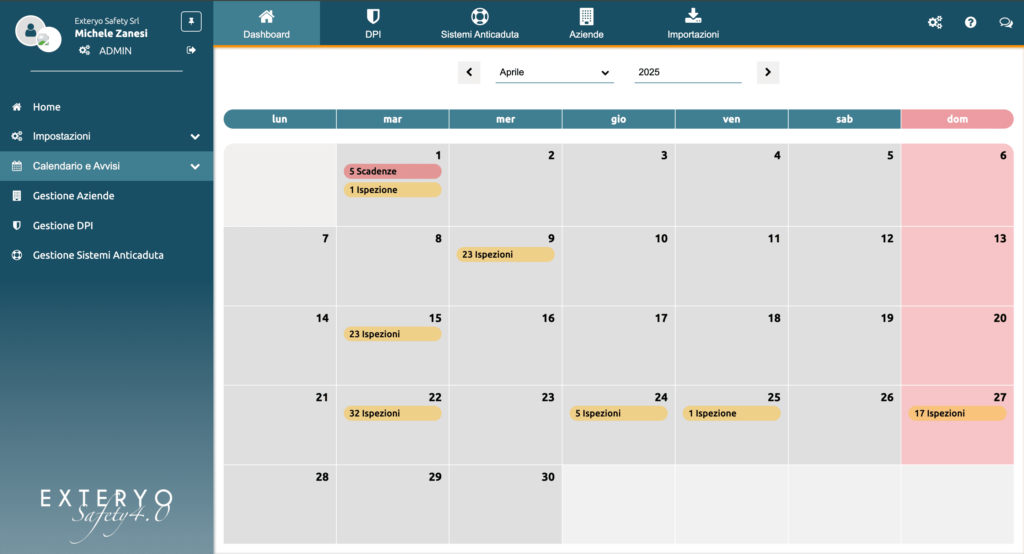
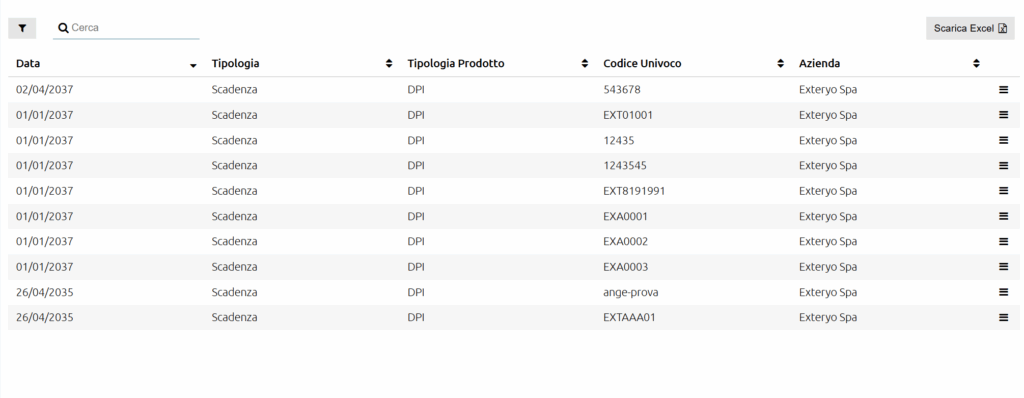
6.12 ITEMS - EVENTS
The EVENTS section in the CALENDAR AND ALERTS menu summarises every single activity related to the devices you manage.
The types of events recorded are periodic inspections, device life expiry dates or any customised alerts recorded during inspection or repair.
7. SYSTEMS MANAGEMENT
7.1 SYSTEMS MANAGEMENT – HOME
The SYSTEMS MANAGEMENT section groups together all the functions that allow you, as the company manager, to control and manage the status of your company’s systems (and related components), as well as to check their periodic inspections and any repairs, and to check any deadlines.
In the HOME function of the SYSTEMS MANAGEMENT section you can set up ACTIONS and WIDGETS to support your activity.
To learn how to manage these tools, please read the appropriate section of the ACTIONS AND WIDGETS tutorial.
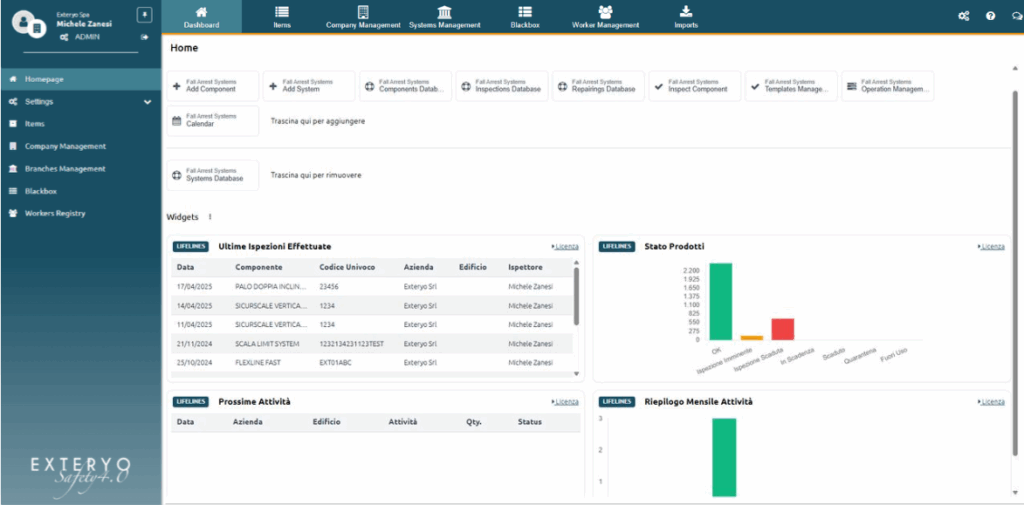
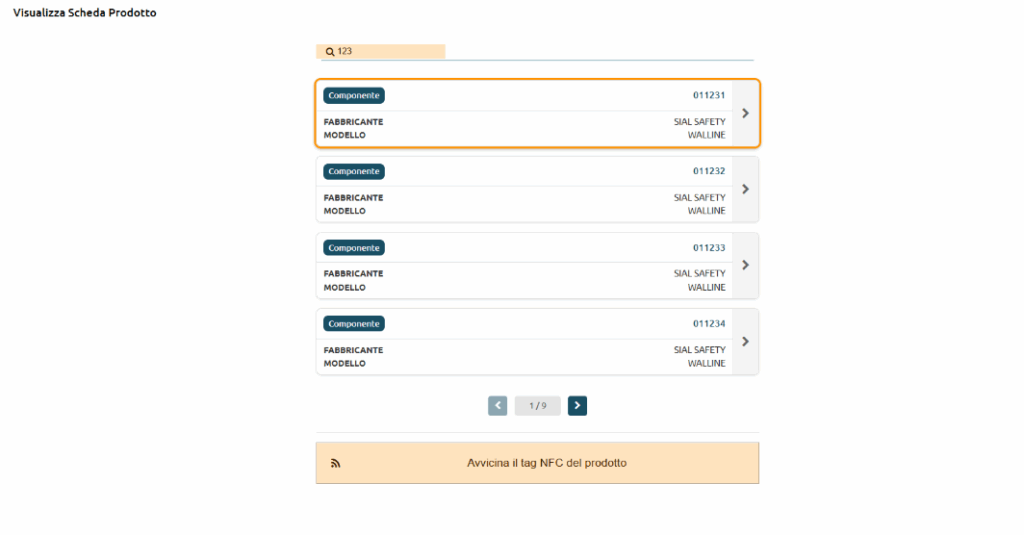
7.2 SYSTEMS MANAGEMENT – SCAN ITEM
The read product function allows you to access the specific product sheet of a SYSTEM or a specific COMPONENT that you manage, by reading the appropriate digital identifier (NFC/Qrcode) or by entering the unique product code manually.
Unlike the OPEN PRODUCT SHEET function on the Log-in page, the SCAN ITEM function gives you access to all product data, including the data of the company that owns the system or the specific component.
7.3 SYSTEMS MANAGEMENT – SYSTEMS REGISTRY
Within the REGISTRIES menu, the SYSTEM REGISTRY function provides an overview of all SYSTEMS in the company and managed by a synchronised inspector.
For each System, the main characteristics are shown in the table, including the data of the branch on which they are installed.
The last column of the table shows the status of the system in different colours. The system status options are derived from the statuses of the individual components and are as follows:
OK (green colour) : there are no component warnings
EXPIRY (yellow colour) : an expiry date within 30 days (periodic inspection) of at least one of the components of the installation has been found.
EXPIRED (red colour) : an inspection deadline has passed for at least one of the system’s components.
TO BE REPAIRED – USEFUL: At least one of the components of the installation has had an inspection with outcome TO BE REPAIRED but it has been indicated that it can still be used.
MUST BE REPAIRED – NOT USEFUL: At least one of the system components has had an inspection with the outcome MUST BE REPAIRED and must not be used.
OUT OF USE: At least one of the components of the system has received a negative result at the last inspection or has been specifically put out of use.
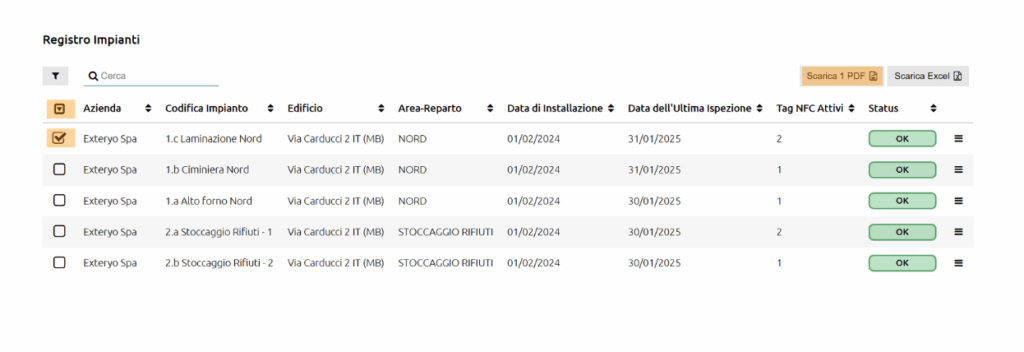
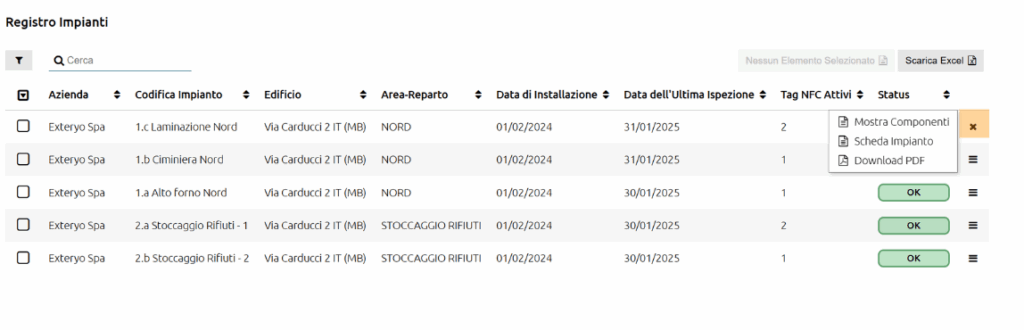
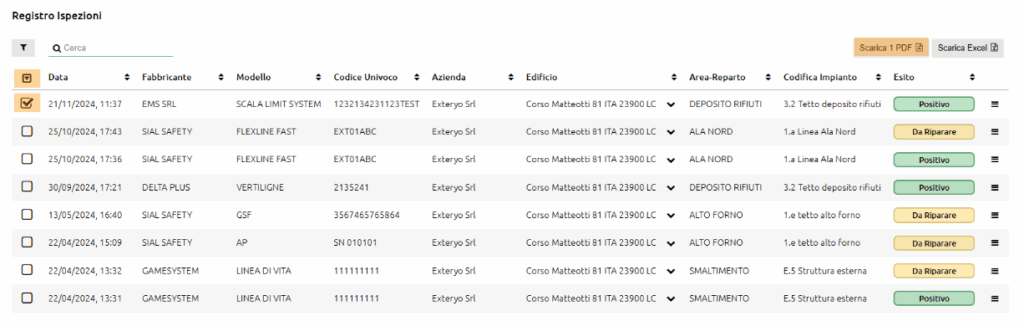
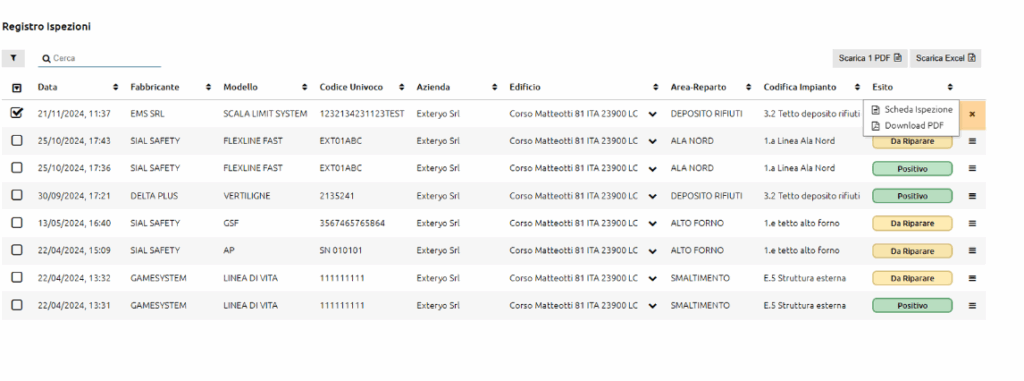
7.4 SYSTEMS MANAGEMENT – INSPECTION REGISTRY
Within this table, inspections of company system components will be displayed.
Inspections can be managed by an external inspector using his dedicated Exteryo Safety 4.0 licence.
By clicking the button, it will be possible to view the relevant inspection sheet or to download a PDF of it.
It is also possible to add inspections manually by clicking the ADD INSPECTION button and entering the unique product code (or reading the digital identifier).
Then simply enter the required data from the form and attach the inspection document.
7.5 SYSTEMS MANAGEMENT – REPAIRS REGISTRY
In this table, repairs to company system components can be displayed.
Repairs can be managed by an external inspector using his dedicated Exteryo Safety 4.0 licence.
By clicking on the button, it will be possible to view the respective repair record or download a PDF of it.
It is also possible to add repairs manually by clicking the ADD REPAIR button and entering the unique product code (or reading the digital identifier).
The system will only allow the management of those devices that have received a result TO BE REPAIRED in a previous inspection.
Then simply enter the data requested in the form and attach the inspection document.
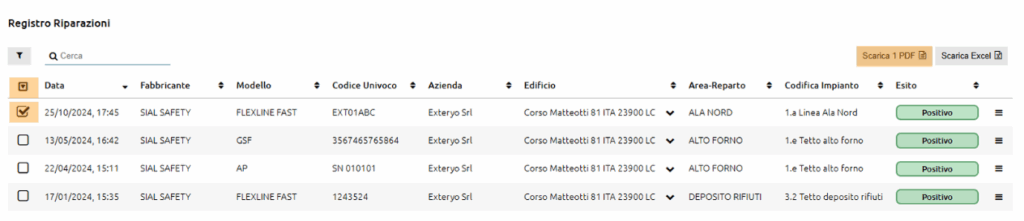

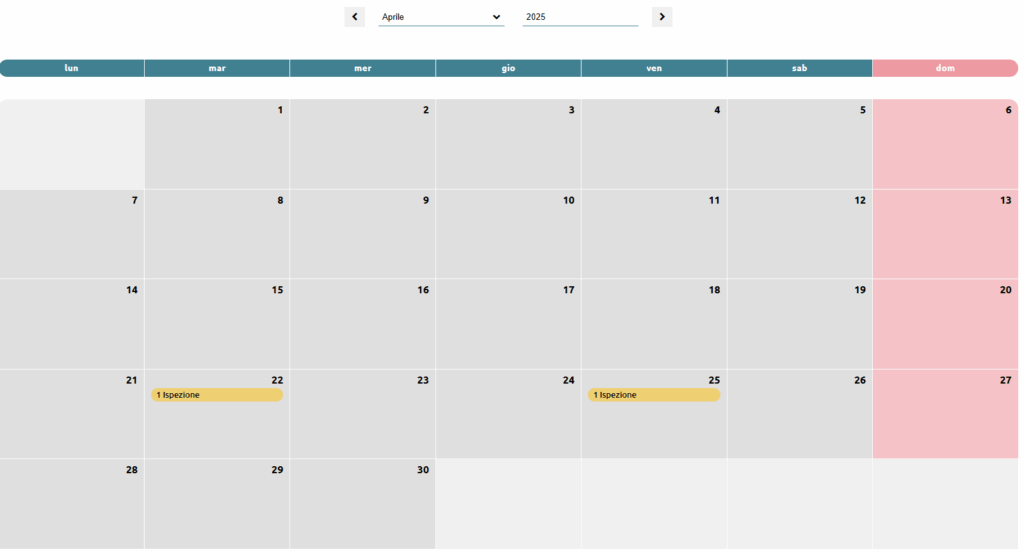
7.6 SYSTEMS MANAGEMENT – CALENDAR
Within the CALENDAR AND ALERTS menu you can access the CALENDAR function through which you can have a visual report of the different activities organised month by month.
By clicking on a specific notice in one of the calendar dates you will be directed to the EVENTS function already filtered for that specific day and that specific activity, so that you can get more details on the planned activity.
7.7 SYSTEMS MANAGEMENT - EVENTS
The EVENTS section in the CALENDAR AND ALERTS menu summarises every single activity related to the devices you manage.
The types of events recorded are periodic inspections, device life expiry dates, or any customised alerts recorded during inspection or repair.
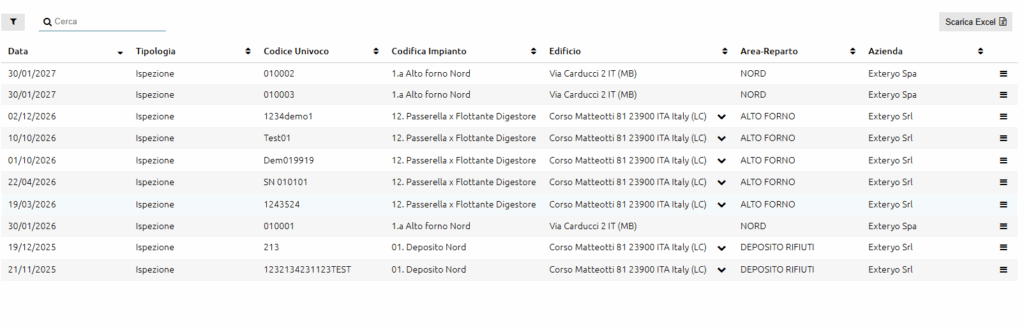
8. COMPANY MANAGEMENT


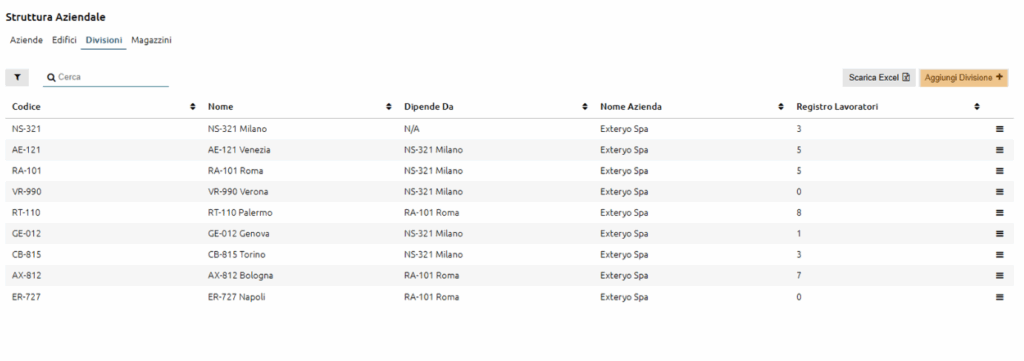
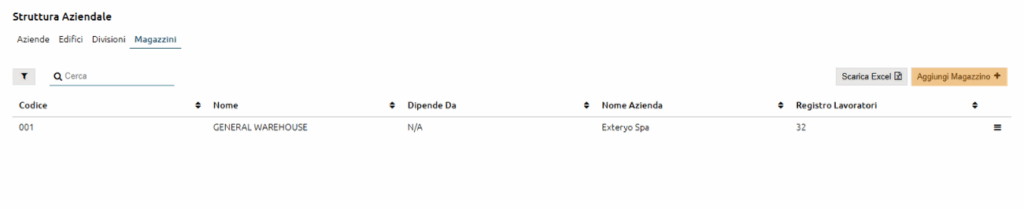
8.1 COMPANY SCRUTRURE
Within the section COMPANY STRUCTURE you can manage all the data relating to the organisation of your company.
In detail, it is possible to add data on these facilities:
COMPANIES: In this section, several companies can be added for which security management is centralised. This option is especially useful for large companies with a diversified company structure.
BRANCHES: In this section it is possible to add and manage data relating to company branches/establishments. Once a new branch has been created, by clicking the button at the end of the relevant line, it is possible to select the option ADD PLANIMETERS, to add up to 3 planimetries of the branch, which can be accessed by platform users (internal or external inspectors) if required.
DIVISIONS: In this section, it is possible to add the various company divisions (or cost centres) and associate them with their controlling company.
In addition, it is possible to create hierarchical dependency relationships, which are essential for the display of specific information by the various users, according to their assigned role.
WAREHOUSES: In this section it is possible to add the various company warehouses authorised to supply/receive security devices. It is also possible to associate a dedicated factory to each warehouse.
8.2 DUTIES REGISTRY
Within this function it is possible to generate the company duties, which is essential for associating the right information to each worker.
To add a new duty, click on the ADD DUTY button and enter the relevant reference code, the duty description and the companies with which the duty is associated.
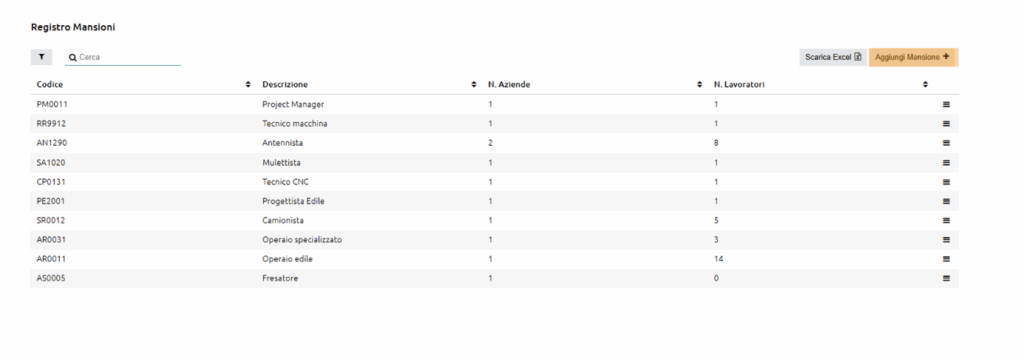
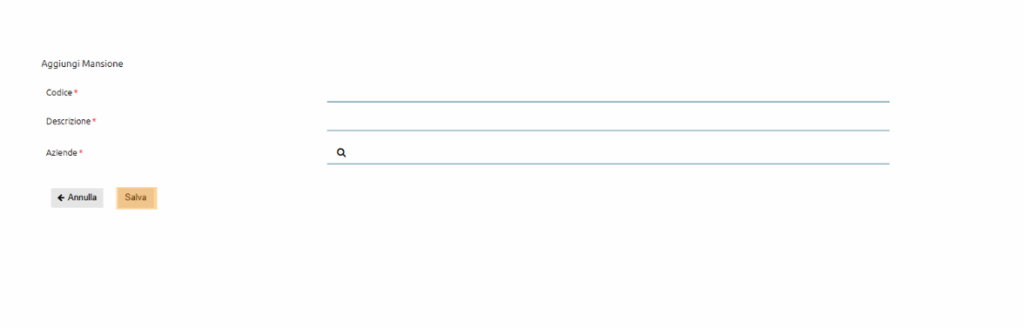
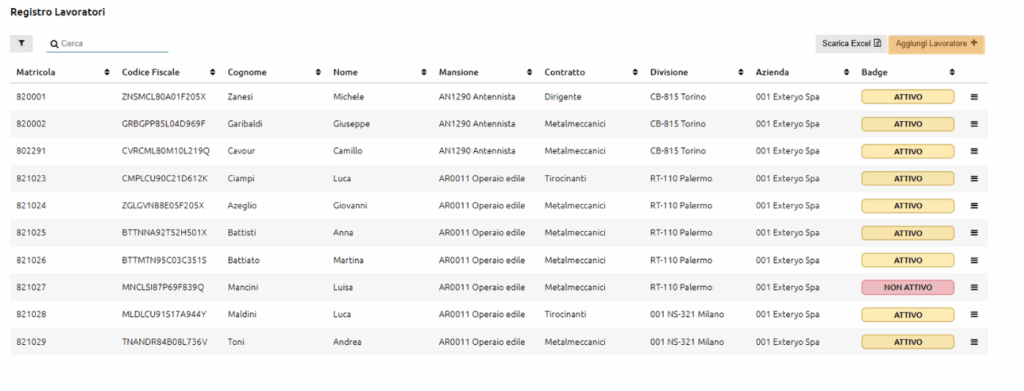
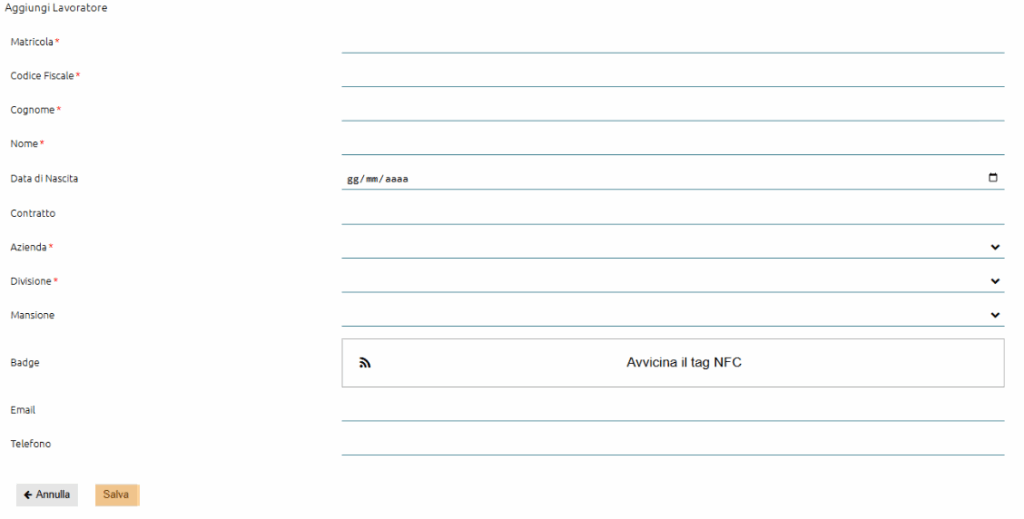
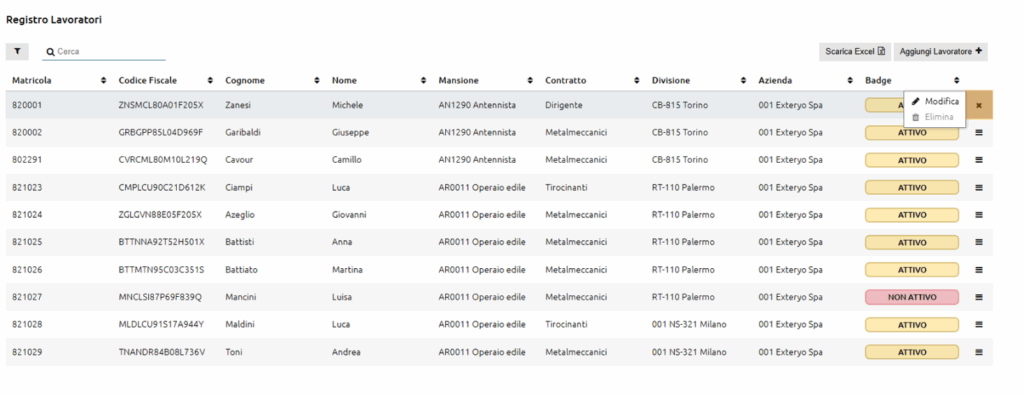
8.3 WORKERS REGISTRY
Within the worker Registry, you can manage all company workers for whom the relevant safety activities will be handled by the platform.
To create a new worker, click on the ADD WORKER button and then complete the form with the relevant data.
In the data entry phase, it is already possible to also associate the badge relative to the worker and useful both for the log-in phase via badge, and for the eventual signature via badge (if foreseen by the appropriate option on the PREFERENCES page).
If the employee’s e-mail address is entered, an e-mail will automatically be sent to his or her mailbox at the time of creation, providing the appropriate credentials to access the platform.
9. BLACK BOX
9. 1 BLACK BOX MANAGEMENT
The black box is the tool provided by the platform for storing and archiving all activities and documents relating to company safety at work and carried out via Exteryo Safety 4.0.
By using the Black Box, it is therefore possible to chronologically reconstruct the course of all activities relating to the lifecycle management of a device, or of a fall arrest system, or of the activities relating to a specific worker and plant.
The black box table consists of a date/time column, a column indicating the macro-activity recorded and one relating to the activity specifications.
The penultimate column relates to the certification key, i.e. the indication provided by the plate that the data recorded actually represents the activity performed without any modification of that data.
Finally, the last column relates to the document demonstrating the activity performed, where available.
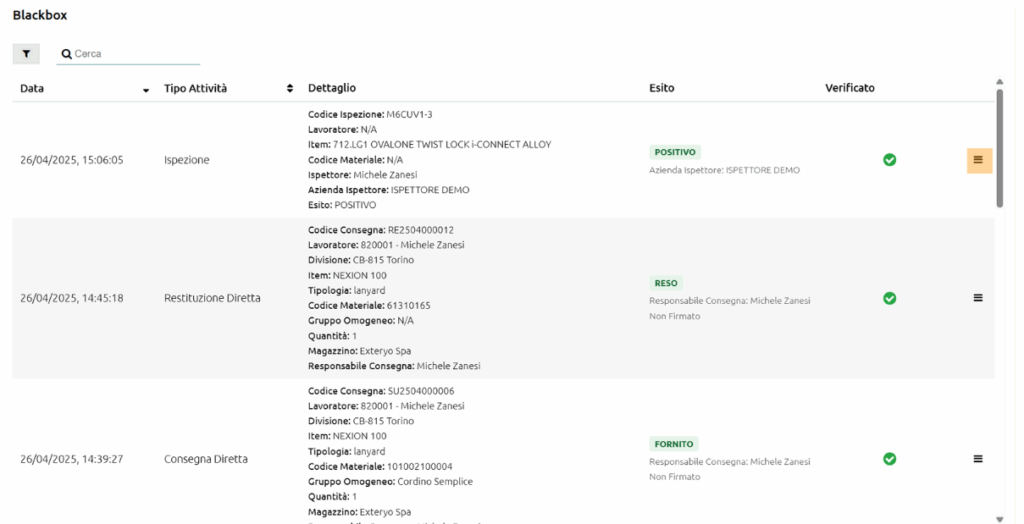
10. WORKERS MANAGEMENT
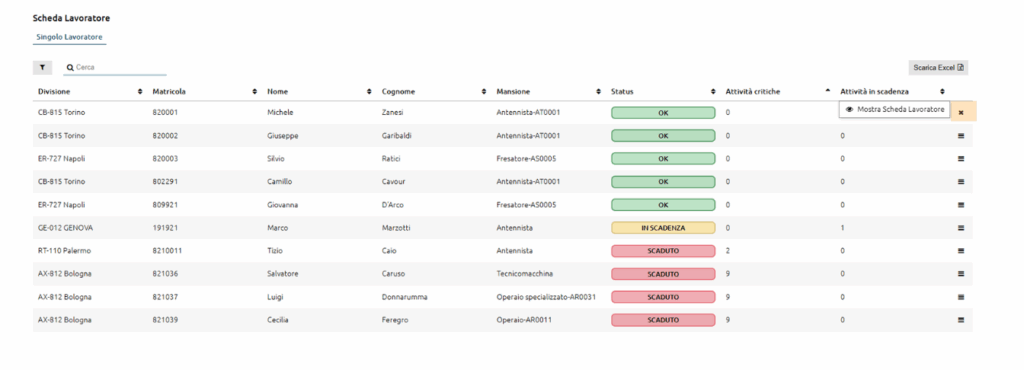
10.1 WORKER DATA SHEET
The WORKER MANAGEMENT section contains the functions that enable the direct control and management of the worker’s safety status and related management and control activities.
The first of these features is the WORKER SHEET, which is the section where the safety statuses and related information of both individual workers and company divisions are highlighted.
With regard to the SINGLE WORKER, the table provides a direct overview of the worker’s security status, highlighted with a specific colour within the STATUS column.
If there are devices in the worker’s possession with an expiry date that has already passed the life cycle or inspection date, the status will be highlighted in red with the word EXPIRED and the exact number of indicated expired products in his possession will appear in the EXPIRED column.
If, on the other hand, the worker is in possession of devices that are due to expire within the next month, the status will be highlighted in yellow with the word EXPIRING, and the related column EXPIRING will show the count of devices that have a scheduled activity within 30 days.
By clicking on the button at the end of the worker’s row, the option SHOW WORKER SHEET can be selected, in order to obtain a more detailed overview of the safety status of the specific worker.
The individual worker sheet consists of a first general section in which the personal and business management data of the individual worker are indicated and, further down, the details of all critical and expiring activities relating to the worker.
In the PPE and WORKWEAR section, on the other hand, the individual devices in the worker’s possession are highlighted, with a specific indication of first use and expiry date, as well as health status.
With regard to the DIVISION, the table behaves in the same manner as displayed for the worker, but offering a complete overview of the notices for all workers belonging to that specific division.
This activity is essential in order to have complete control of all workers within a single page and to be able to intervene promptly to solve any problems.
Again, by clicking the button and selecting SHOW DIVISION DETAILS, it is possible to have a detailed overview of the general information of the division, but also of the PPE and workwear in the possession of the workers belonging to that specific division.
10.2 BADGE MANAGEMENT
The BADGE MANAGEMENT function allows a company manager to control and activate the workers’ badges required to allow the worker access to his or her own dedicated area of the platform, or to sign documents (after choosing the option to sign with a badge within the PREFERENCES in the GENERAL SETTINGS section).
To assign a badge to a worker using this function, click on the button at the end of the worker’s line and select the ASSIGN BADGE item.
Then place the badge on the back of your phone or on the NFC reader for PC to enable pairing. Once associated, the heading ACTIVE will appear in the BADGE STATUS column.
If it is necessary to remove the badge, choose the REMOVE BADGE item from the button. Once removed, the status badge will read NOT ACTIVE.
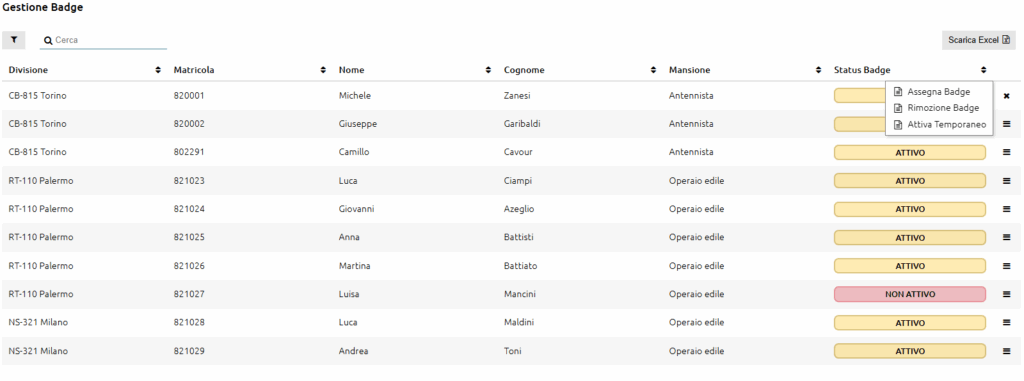
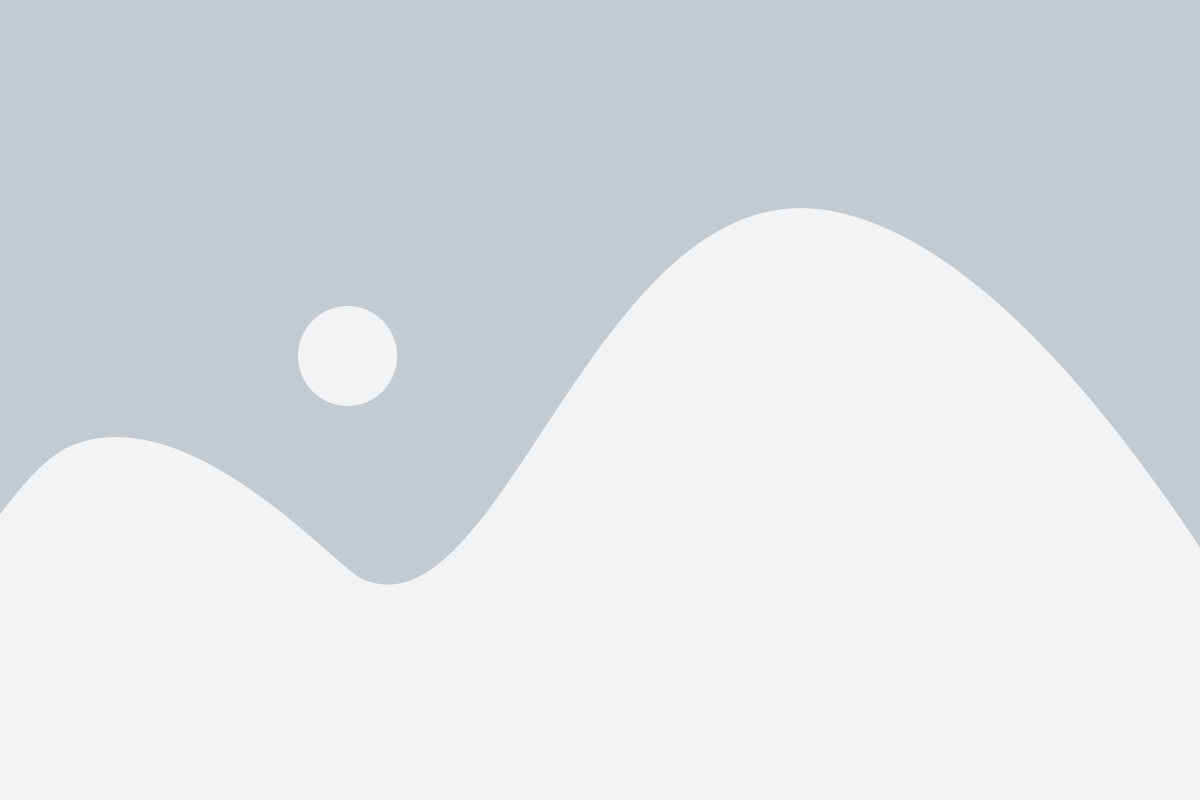
10.3 FAST CHECK
La funzione FAST CHECK permette ad un responsabile dell’azienda di poter effettuare un rapido audit nei confronti di un lavoratore per il controllo dell’utilizzo dei dispositivi da parte di quest’ultimo e per il controllo dello status di salute degli stessi dispositivi.
Per effettuare un nuovo audit ad un lavoratore, cliccare il tasto posto al termine della riga relativa ad un lavoratore e selezionare la voce
controllare e attivare i badge dei lavoratori necessari per permettere l’accesso del lavoratore alla propria area dedicata della piattaforma INIZIA AUDIT.
A questo punto si aprirà il report di Audit nel quale saranno presenti le seguenti sezioni:
INFORMAZIONI GENERALI: indica le informazioni dettagliate del lavoratore e del responsabile che sta effettuando l’audit.
REPORT: mostra la lista di tutti i dispositivi in possesso del lavoratore e per ognuno dei quali è possibile indicare se il lavoratore sta indossando o non indossando il dispositivo durante l’attività, oppure non è necessario l’utilizzo durante l’attività svolta.
ESITO FINALE E PERSONALIZZAZIONI: Al di sotto della checklist è presente con due tasti colorati l’esito finale da indicare per l’audit effettuato, scegliendo tra POSITIVO e NEGATIVO.
Al di sotto dei riquadri relativi all’esito di ispezione è possibile inserire le seguenti personalizzazioni dell’audit:
– FOTO : Possibilità di aggiungere foto dedicate dell’audit effettuato
– NOTE: Possibilità di aggiungere una nota dedicata per l’audit effettuato
– FIRMA DEL LAVORATORE: Spazio di inserimento della firma da parte del lavoratore
– FIRMA DEL RESPONSABILE DEL CONTROLLO: Spazio di inserimento della firma del responsabile del controllo dell’audit.
Una volta conclusa l’attività, cliccare su SALVA per salvare l’audit nel sistema.
11. IMPORTING DATA INTO THE SYSTEM
11.1 IMPORTING DATA
In order to facilitate massive data entry within the platform, especially in an initial phase of use, you can use the options in the IMPORT section.
Within this section, the import functions are divided into two groups:
– COMPANY IMPORTS
– DEVICE IMPORTS
Within each group there are several import options.
Once you have identified the desired import option, click on the DOWNLOAD TEMPLATE button to start downloading the excel file template in which to enter the data.
After compiling the EXCEL file, you can start the import by selecting the EXCEL file from the CHOOSE FILE button.
If some data are not recognised by the system, they will be highlighted in red, giving you the possibility to modify them.
Once you have completed the checking phase, click on the SAVE IMPORT button to confirm the activity.
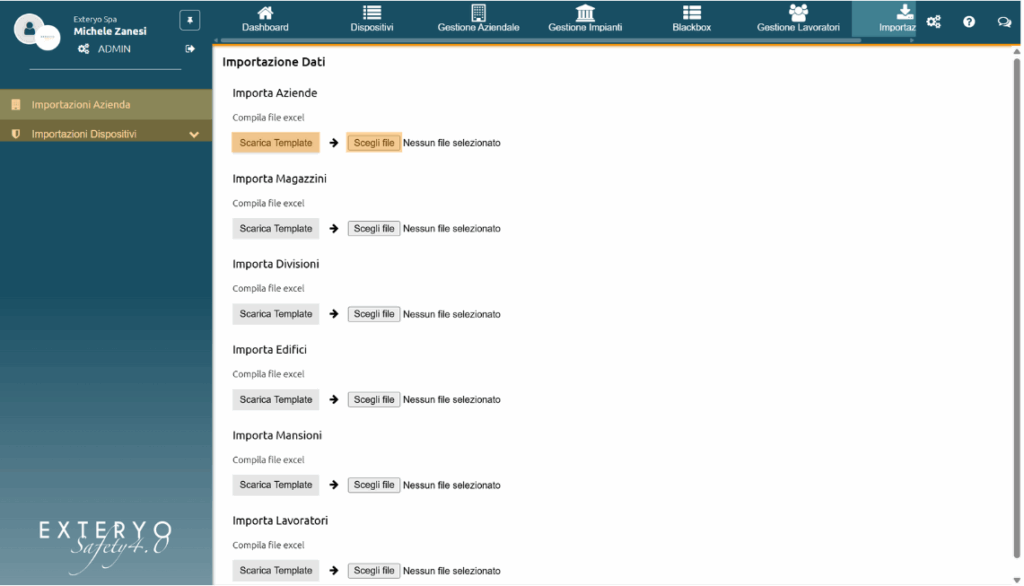
12. WORKER ACCESS
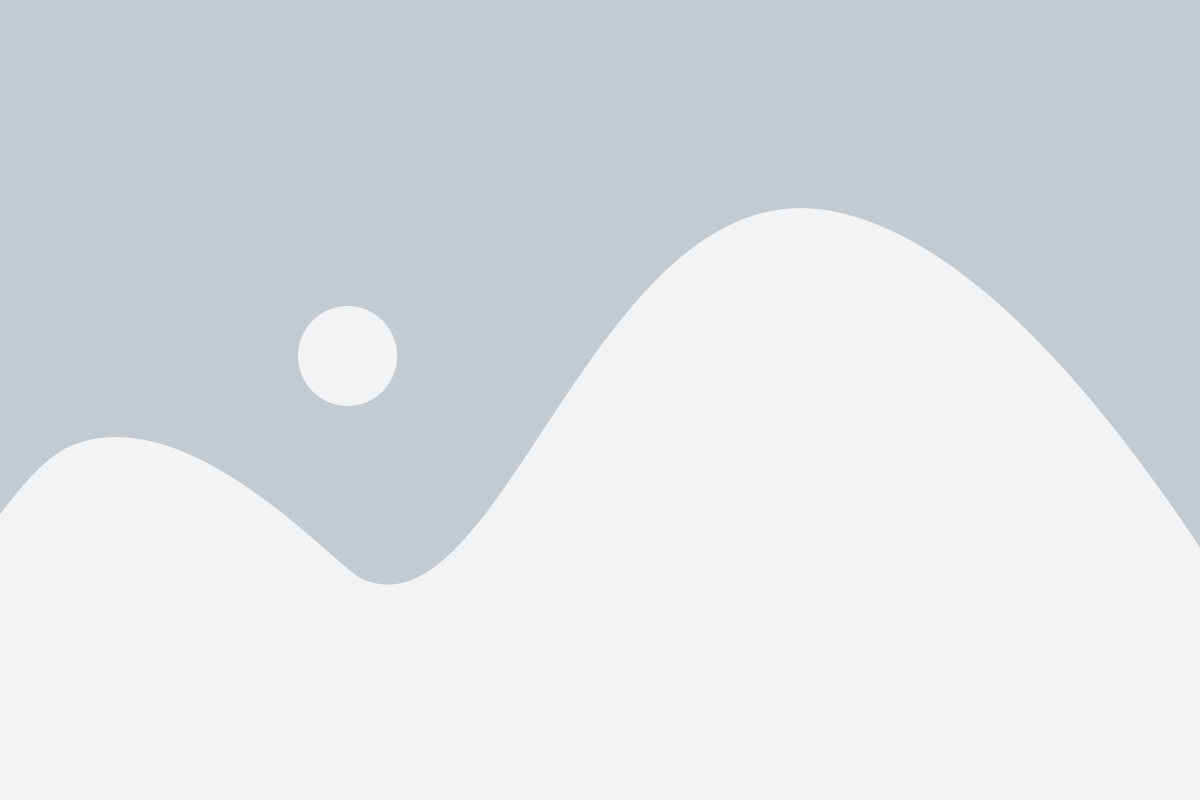
12.1 SCHEDA LAVORATORE
L’accesso lavoratore è un insieme di funzionalità previste per i singoli lavoratori mediante le quali potranno avere accesso in trasparenza al proprio status di sicurezza e gestire specifiche attività nella consegna e reso dei dispositivi.
La prima di queste funzionalità è la SCHEDA LAVORATORE che permette la lavoratore di avere visualizzazione della propria scheda informativa relativamente ai dispositivi (DPI e abbigliamento) in suo possesso.
La scheda si compone di una prima sezione generale in cui sono indicati i dati anagrafici e di gestione aziendale del lavoratore e, più in basso, le indicazioni puntuali di tutte le attività critiche e in scadenza relative al lavoratore.
Nella sezione DPI e ABBIGLIAMENTO invece sono evidenziati i singoli dispositivi in possesso del lavoratore con la specifica indicazione delle attività di primo utilizzo e scadenza, nonché lo status di salute.
12.2 DELEGATED SUPPLY
The DELIVERY BY DELEGATION function allows the individual worker to be able to check the list of any devices received through the delegation entrusted to another worker and at the same time be able to sign the related delivery report.
Whenever the delegated delivery of one or more devices is defined (see the appropriate function in section 6.4 ITEMS-SUPPLY), this can be displayed in the table with the data relating to the Date of the delegated delivery, the name of the delegate and the activity status.
Clicking on the button and selecting the MANAGE DELIVERY option will display the final delivery report that the worker must sign using the method (calligraphy or badge) defined by the company.

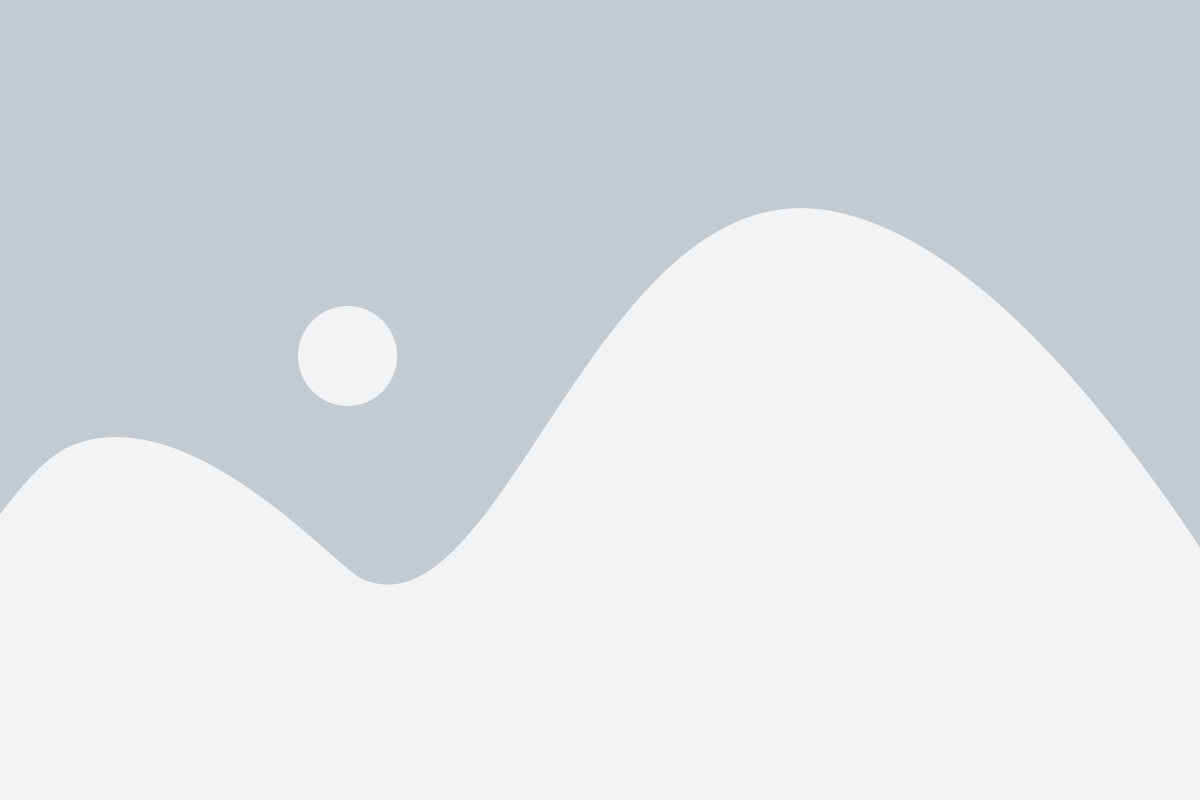
12.3 RESO IN DELEGA
La funzione RESO IN DELEGA permette al singolo lavoratore di poter controllare la lista di eventuali dispositivi da dover rendere mediante la delega affidata ad un’altra lavoratore e contestualmente poter firmare il report di reso relativo.
Ogni qual volta che viene definito un reso in delega di uno o più dispositivi (vedi apposita funzione nel paragrafo 6.5 DISPOSITIVI-RESO), questo potrà essere visualizzata all’interno della tabella con i dati relativi alla Data del reso in delega, il nominativo del delegato e lo status di attività.
Cliccando il tasto e selezionando l’opzione GESTISCI RESO verrà visualizzato il report di reso finale che il lavoratore dovrà firmare mediante la modalità (calligrafica o badge) definita dall’azienda.